Custom photo printing has enabled diverse industries and creatives to achieve their vision through customized photo media that offers flexibility beyond conventional stock to precisely meet project needs.
Introduction
Custom photo printing has grown in demand from various industries and creative professionals. Rather than conventional photo papers that come in standard formats and finishes, custom photo media offers flexible specifications tailored to individual needs.
Users can customize aspects like thickness, texture, dimensions and other properties to precisely suit intended applications. This level of customization is important for many photography and design use cases.
Professional photographers rely on tailored paper choice and sizing for high-quality exhibition and portfolio prints that make their work stand out. Brands and exhibitors also depend on customized photo materials to create striking commercial displays at events, in-store, and for outdoor advertising.
Other common applications needing specialized photo options include commemorative projects, art prints, self-publishing, and customized stationery or gift wraps. Rather than off-the-shelf stock, these projects require photo prints and media manufactured to technical specifications defined by the creator or client.
The expanded possibilities of custom photo printing have proven invaluable for diverse industries and creative fields. Being able to tailor paper mediums provides the flexibility and control photographers, designers and businesses need to successfully achieve their vision.
Pillar 1: Material Selection
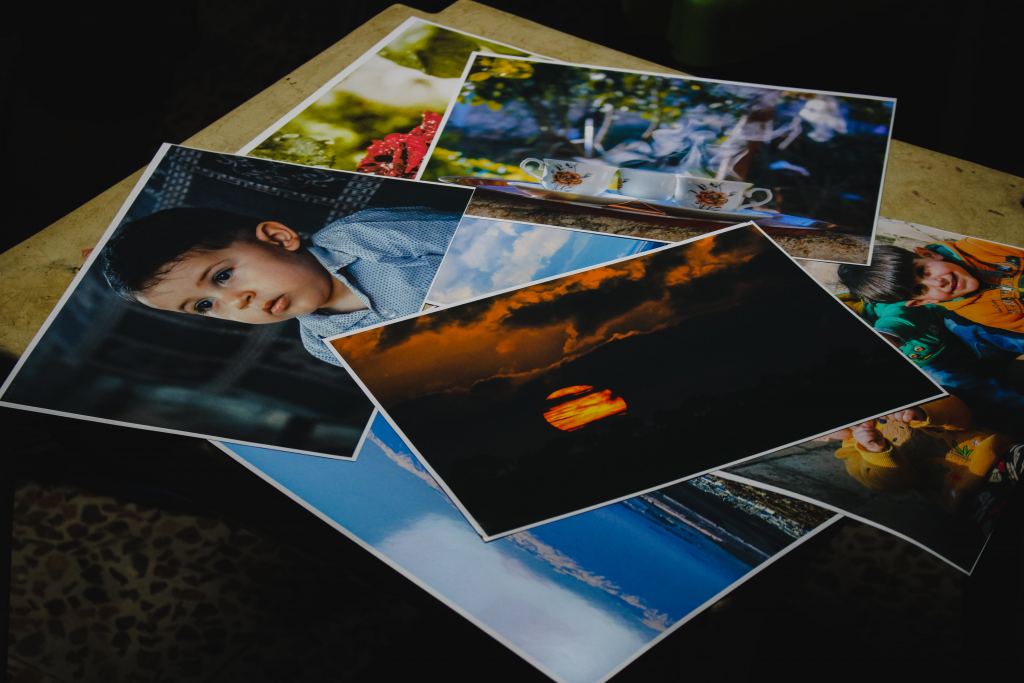
● Different Types of Photo Paper Materials
There are several photo paper options available for customized printing projects. Three of the most popular types are resin-coated paper, fiber-based papers, and synthetic papers.
Resin-coated paper features a polyethylene layer coated onto a paper substrate. This provides it with superb moisture resistance and durability. It reproduces sharp images well-suited for high-quality prints.
Fiber-based papers like cotton yield soft textures and natural color rendition. However, they have less water resistance compared to other varieties.
Synthetic papers are comprised of polyester materials. They excel at weatherproofing and resisting tears or punctures. Such properties make them very suitable for outdoor displays subjected to environmental conditions.
All of these paper types – resin-coated, fiber-based, and synthetic – cater to different needs depending on the intended application and required paper qualities. Their varying properties allow photographers and graphic designers to choose photo media tailored to each customized printing project.
● How to Select the Suitable Material Based on Project Needs
Choosing the right materials is essential to fulfilling client needs. Factors to evaluate involve intended use, budget, expected lifespan, display environment, and finishing requirements.
For instance, resin papers excel for gallery shows but may cost more than fiber-based options for high volume jobs. Synthetic papers like Tyvek can withstand rough conditions but lack the fine detail needed for portraiture.
Clear communication with clients is key to understanding technical specifications and balancing priorities. Showing material samples allows clients to visualize choices before deciding.
Wholesalers should recommend alternatives while considering their production capabilities. Suggesting added services like lamination provides value too. The goal is finding solutions that meet clients’ requirements within budget, and advising on paper properties, potential applications and complete solutions.
With input from clients and factoring printing needs, wholesalers can propose the most suitable paper and related services for each customized project. Meeting technical specs is important, but so is offering attractive value.
● Material Affects Quality, Applications, Price etc.
The choice of paper significantly affects the final output. More resilient materials help maintain image quality for extended periods of use. Acid-free and archival options prevent discoloration over time. Texture can enhance the viewing experience. Waterproof versions protect prints in wet environments. Heavier paper weights convey a sense of quality.
Generally, specialized characteristics and non-standard sizes increase cost. Paper serves as the foundation for high-quality customized outputs. Staying within budget objectives is also important.
In summary, material selection lays the groundwork for achieving goals related to both quality and affordability. The importance of choosing the right paper should not be overlooked, as it directly impacts how well the final product fulfills its purpose in its intended setting and lifespan. Accounting properly for the type of paper used is vital to client satisfaction.
Pillar 2: Design Details
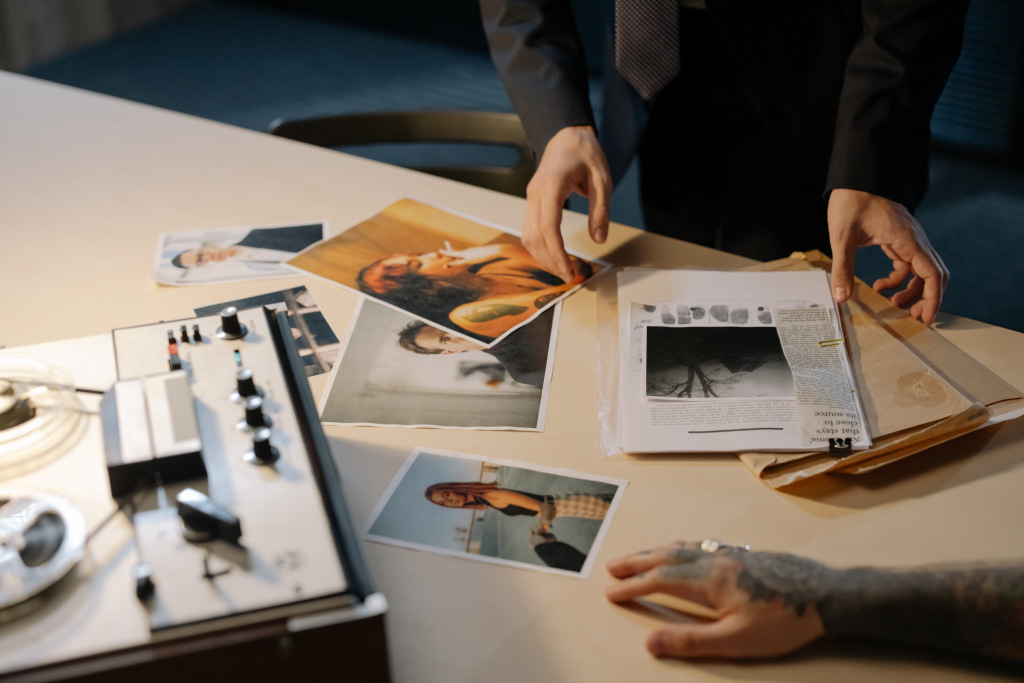
● Graphic Design is Key to Custom Print Quality
The graphic design process for customized prints significantly influences the final aesthetic and reception. As each design is unique, meticulous attention to design details is paramount. Even a slight misalignment or color shift could compromise an otherwise perfect piece.
Those creating custom designs require proven proficiency in key areas such as layout, typography, image optimization, and color accuracy. Principles of design structure, hierarchy, flow and balance must be thoroughly understood and applied. Images need to be properly sized, cropped, optimized and profiled for best output quality. Typefaces should complement the design concept and content.
Precise color management from image editing through printing is also vital. Colors must be calibrated to display and print accurately across all mediums and print profiles. Quality control checks at various stages help catch and fix issues before final production.
Only by mastering fundamental design skills and leveraging professional tools can high-level customized graphical content be reliably produced to the standard expected by discerning clients. Satisfying their vision demands technical design excellence.
● Discuss Elements like Image, Layout, Color Matching
Image quality is paramount, especially for enlarged prints. Using high-resolution digital files without pixelation is critical.
Layout effectiveness depends on focal elements catching the eye appropriately based on the context. Whether close-up desk frames or long-distance billboards, the design must complement the intended viewing conditions.
Readability matters greatly for text-heavy designs. Proper font selection and sizing helps ensure legible transmission of information.
Consistent, accurate color from design to printed output hinges on monitor calibration according to industry standards like SWOP. Even minor hue or tone mismatches can negatively impact perceived quality.
It is also important to consider substrate color interactions – how images appear on white paper differs from transparent materials. Subtle substrate effects must be anticipated.
Mastering such nuanced factors related to resolution, composition, typography, color management and paper properties allows fully realizing clients’ custom design visions across diverse printing applications. Paying close attention to detail yields optimal results.
● Examples of Good and Bad Design Practices
Effective designs establish visual hierarchy through repetition, proportion, and balanced spacing. Overly busy layouts reduce focus, whereas breathing room allows certain pieces to stand out. Consistent style maintains cohesion across related works.
Technical preparations such as rasterizing vector graphics and flattening layers expedite print production. Not doing so can introduce issues.
Potential missteps involve improperly sized or mismatched elements that disrupt flow. Difficult-to-read serif fonts diminish legibility for large-scale viewing. Unoptimized, bloated files drive up costs and time. Uncalibrated soft-proofs misrepresent final printed results.
Attention to fine details throughout the design and pre-press stages helps avoid such pitfalls and fully realizes the creative vision on paper. It is as much an art as a science to satisfy customized printing needs. Mastering design principles, technical aspects and quality control yields optimized final outputs meeting client expectations. Taking a holistic, conscientious approach reaps the greatest rewards.
Pillar 3: Production Technology
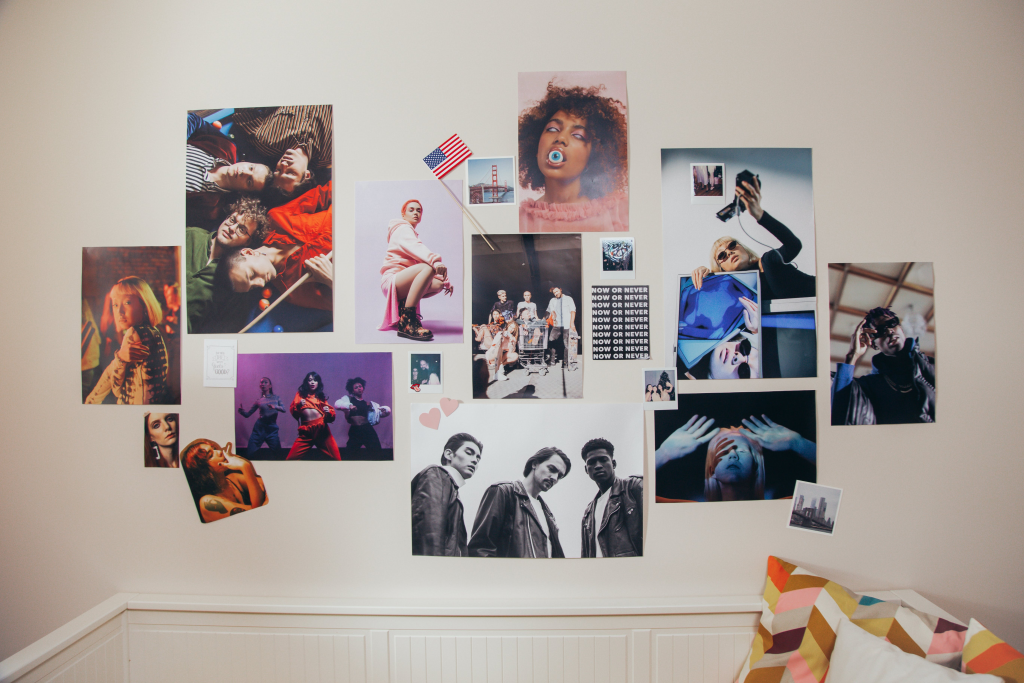
● Digital printing and Sublimation Process
Two prevalent production techniques for customized prints are inkjet printing and dye sublimation. Inkjet utilizes printheads to deposit pigment or dye inks directly onto substrates. Dye sublimation applies heat to transform dye from solid to gas phase, allowing its absorption into substrate fibers in bright, fade-resistant form.
Both require carefully calibrated machinery and environmental conditioning for output consistency. Operators must undergo specialized training to competently manage the many technical process variables inherent in these technologies. Even minor fluctuations in parameters like temperature, pressure or ink density can compromise results.
To reliably satisfy clients, operators must demonstrate proficiency in their chosen production method. Only by maintaining strict protocol through rigorous quality control measures and device calibration schedules can the required level of print accuracy and uniformity be achieved time after time. Satisfying demanding custom jobs demands expert handling of sophisticated production equipment.
● Emphasis on Process Control and Quality Standards
Quality assurance is imperative since even subtle variances can induce defects. Standard operating procedures promote consistent performance over time despite changes to operators or shifts. Calibrations employing specialized equipment help optimize settings like droplet size and density.
Careful process monitoring guards against medium to long-term issues caused by drift in critical factors such as temperature, pressure and drying uniformity. Automation assists in upholding tight production specifications.
Routine audits identify any process deviations or opportunities for enhancement. Regular equipment calibrations, quality checks and monitoring prevent defects by catching and correcting minimal drift from standardized methods. Compliance with prescribed quality control protocols provides assurance customized outputs consistently fulfill clients’ expectations. Only through diligent adherence to best practices can the highest production standards be maintained.
● Ensuring Consistency across Mass Production
Meeting quality standards for high-volume customized orders introduces specific challenges. Establishing baselines through sampling is important before undertaking larger production runs. Inline inspection allows for timely identification of potential issues.
Statistical process controls involving representative sampling check for conformity while also helping detect assignable and common sources of variability as a preventative measure.
Consistency in materials handling, packaging and shipping safeguards the finished products. Adherence to rigorous manufacturing protocol and quality procedures ensures clients receive an outstanding product experience regardless of order size.
Close monitoring and statistical process analysis help identify and correct potential factors jeopardizing consistency as quantities increase. Through application of sampling, inspection, documentation and change control practices, specification compliance at scale is achievable.
Conclusion
Producing high-quality customized photo prints requires balancing 3 pillars:
Material selection – Choosing suitable substrate materials.
Design excellence – Meticulous graphic execution with hierarchy, legibility, color accuracy.
Production mastery – Proficiency in digital/thermal processes through calibration, quality control.
When working with a print lab, clearly communicate needs, vet qualifications, discuss timelines sensibly, obtain final proofs, and maintain open collaboration throughout.
Provide high-quality design files meeting supplier specifications.
To cultivate successful partnerships, suppliers must seamlessly integrate technical expertise with an attentive, customer-centric approach encompassing:
Expertise in substrate, design and production capabilities
Exceptional service through responsive support and issue resolution
An emphasis on post-production assistance and building loyalty
By focusing on skill, service and experience, suppliers satisfy customers, driving positive word-of-mouth and continued market expansion through collaborative relationships.