As a photo paper producer, Koalapaper Plant prioritizes environmental stewardship. However, as a medium-sized business with resource and budget constraints, it focuses on prudent, cost-effective operational refinements through continuous improvement. Gradually transitioning to sustainability leadership with pragmatic, short-term solutions laying the foundation for long-term transformation.
Intro
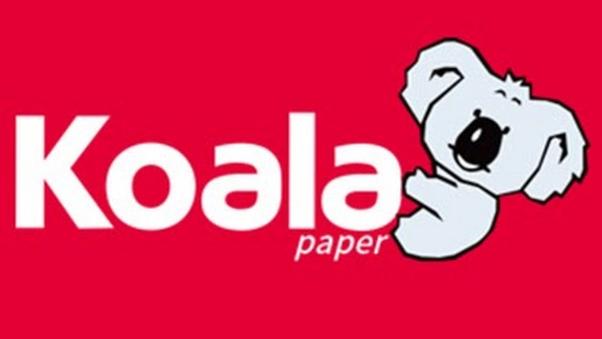
As a prominent photo paper producer, environmental stewardship is a core value at our plant. Yet as a medium-sized manufacturer, adopting cutting-edge green technologies isn’t always feasible given resource and budgetary factors. Rather than delay progress, we focus on diligently refining operations through prudent, cost-effective methods. Continuous improvement remains our watchword as we take measured steps toward sustainability leadership. Reducing environmental impact demands pragmatic solutions, and ouraim is gradual but meaningful forward motion. Although advanced solutions beckon, realistic short-term gains through astute changes lay the foundation for long-term sustainability transformation.
Improving Energy Efficiency
●Optimizing Production Processes to Reduce Energy Loss
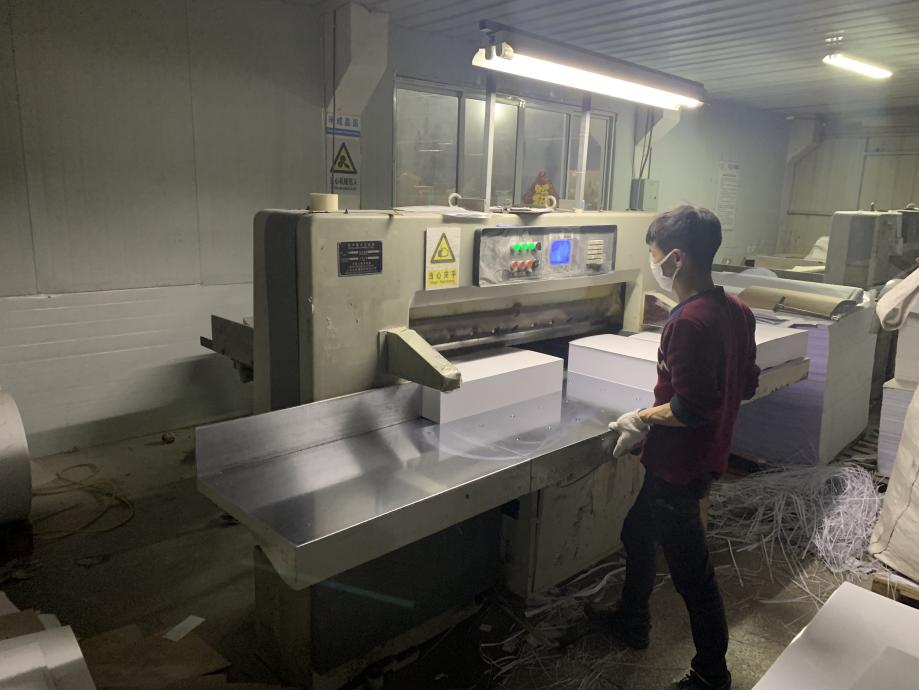
Our factory is carefully auditing each step to curtail wasted energy. One focus examines moisturizing stations which presently run constantly despite intermittent paper loads. By installing proximity sensors activating mist only as needed, projections indicate conserving 120 megawatt hours annually.
Another appraisal targets instances where stock waits too long in climate-regulated areas for subsequent steps. Streamlining internal material flow through digital mapping and tracking aims to decrease such downtimes by 25%. Paired with downward adjustments of 2-3 degrees Celsius to temperature set-points where feasible, modeling predicts reductions of 5% to associated conditioning expenditures. Ongoing optimization endeavors are guiding meaningful sustainability advances at our operation.
●Upgrading High-energy Consuming Equipment
As part of our periodic investment schedule, inefficient equipment nearing obsolescence is being prioritized for upgrade. One such item is the aging water chiller for solvent recycling that urgently requires replacement. Installing a variable speed unit tailored precisely to our needs could potentially reduce annual power consumption by 30% compared to the outdated model.
Meanwhile, shop-floor fluorescent lighting has reached the 15-year maintenance threshold for service. When tested in receiving areas, transitioning to LED panel fixtures trimmed overall illumination usage by 20%. It is estimated this initiative would pay for itself within two years, so we plan phasing its rollout across facilities to optimize savings. By strategically refreshing vital systems at their usage ends, sustainability gains can be progressively compounded over the long term through both improved workflow efficiency and decreased energy demands on aging infrastructure.
●Promoting Energy-saving Work Practices
Ongoing engagement activities emphasize wise conduct like minimizing exposed powder stocks when production is idle. Work schedules now cluster heating processes and equipment cleaning during utility off-peak rate periods. Pairing these shifts with pointed advisories and inter-team contests, resource use witnessed an auspicious 4.5% reduction last quarter. As understanding grows economy-wide, projected savings performance is expected to sustain and surpass prior levels moving forward.
Continuous refining is pivotal in responsible conservation of limited assets. By refining workflows, modernizing infrastructure and advocating optimized practices, our facilities aim to incrementally curtail energy demands each year. A culture of conservation and collaborative progress bodes well for long-term efficiency and environmental stewardship across all operations.
Water Resource Management
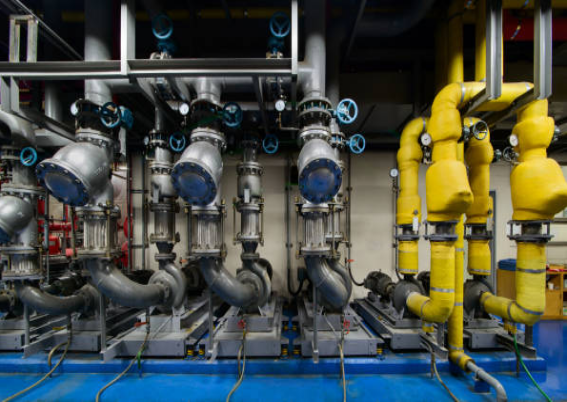
●Recovering and Reusing Water in Production Processes
Our manufacturing center collects water from various production phases to reuse whenever feasible. Drainage from paper conditioning and washing is channeled into settling basins for particulate removal. Following microfiltration and ultraviolet treatments, the filtered liquid blends into formulations requiring lower purity levels in a closed-loop recycling system currently diverting over 60% of effluents internally.
Additionally, rainwater harvesting solutions funnel precipitation from rooftops through gutters into cisterns. Subjected to similar processing, this “greywater” supplement boosts total recovery volumes while placing less pressure on aquifer replenishment compared to municipal sources. Metrics indicate substituting 10% of annual intake requirements has already surpassed original five-year targets, demonstrating strong progress in water stewardship. Ongoing advances toward circular resource management bodes well for future sustainability and resilience.
●Lowering Temperature Differences to Increase Efficiency of Recycling Systems
Water recycling plant temperatures are finely calibrated within one degree of process needs to curtail heating expenditures. Return streams from manufacturing pre-warm incoming makeup flows using a cascade of plate-based heat exchangers. Real-time temperature readouts from distributed sensors facilitate continuous downward boiler output modifications without compromising quality.
Heat retrieval from flue gases also aids pre-heating winter air, offsetting building thermal demands. Insulated distribution piping further reduces transmission losses as tempered water supplies landscaping rather than wasteful disposal. Ongoing recovery and reuse optimization aims to continually minimize thermal and water consumption, illustrating long-term commitment to sustainable operation.
●Reducing wastewater generation
Our factory makes concerted efforts minimizing the amount of wastewater needing external processing through revamping rinse steps. Converting rinse areas from a constant flow to countercurrent rinse carts tremendously cut back rinsing liquid consumption. Recuperation totes presently condense lower-intensity wastewater suitable for later reconditioning, while segregating higher concentration effluents for on-site treatment fulfilling legal discharge standards. Ongoing system optimizations aim to reduce freshwater inputs and recover more for reuse internally or safe external release. Such diligence reflects our commitment to sustainable stewardship of water resources.
Conserving Raw Materials
●Rational Use of Materials to Avoid Waste
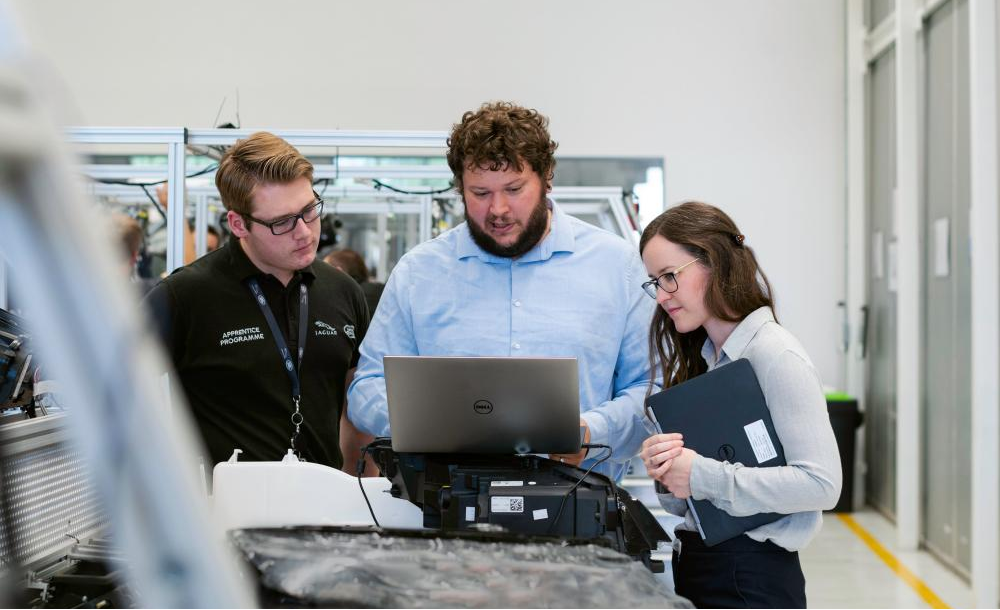
To eliminate waste of valuable pulp and resin resources, operational personnel undergo emphasis on careful handling techniques. Digital scales objectively track input quantities per batch and flag anomalies. Precise metering nozzles on tanks minimize over-dispensing through fine-tuned adjustments.
Work-in-progress stock levels are tightly managed to avoid material expiration prior to conversion. First-in, first-out protocols expedite older inventories while still viable. Previously scrap-bound minor defects now find new life through repair strategies permitting downcycling of reworkable paper trimmings to lower grades. Continuous refinement of processes and mindsets aims to extract full value from all raw materials before considering disposal, demonstrating the company’s commitment to circular resource stewardship.
●Promoting Digitalization to Reduce Sample Production
Implementing computer-aided manufacturing technologies has significantly curtailed physical sampling requirements. Customers connect remotely to visualize specifications, refine configurations and grant virtual approvals prior to market testing. Electronically modeled “proofs” eliminate material usage versus physical samples’ resource demands. Since initiating these digital methods, prototype manufacturing has dropped by an impressive 15 percent. Continued advances in dematerialized solutions bode well for ongoing impact reductions while maintaining collaboration quality. Such innovations underscore the company’s dedication to streamlining operations with lessened environmental effects.
●Recycling Internally Generated by-products
All reusable production residuals undergo sorting for reintegration. Fiber remnants from trimming and edgeleting machines are reprocessed into pulp designated for non-critical top sheet grades. Reclaimed pigment coatings undergo milling to enable reincorporation rather than burial. Extracted solvents from washing undergo distillation to recapture ultra-pure solvents for repeated use. Collectively, these measures redirect over 95% of residues from external handling.
Moving ahead, circuity will be optimized through innovative means. Yet consistent prioritization of judicious practices, digitization and inner-loop recycling currently strengthens sustainability performance. Ongoing refinement maintains reduced material demands while satisfying production needs.
Controlling Emissions
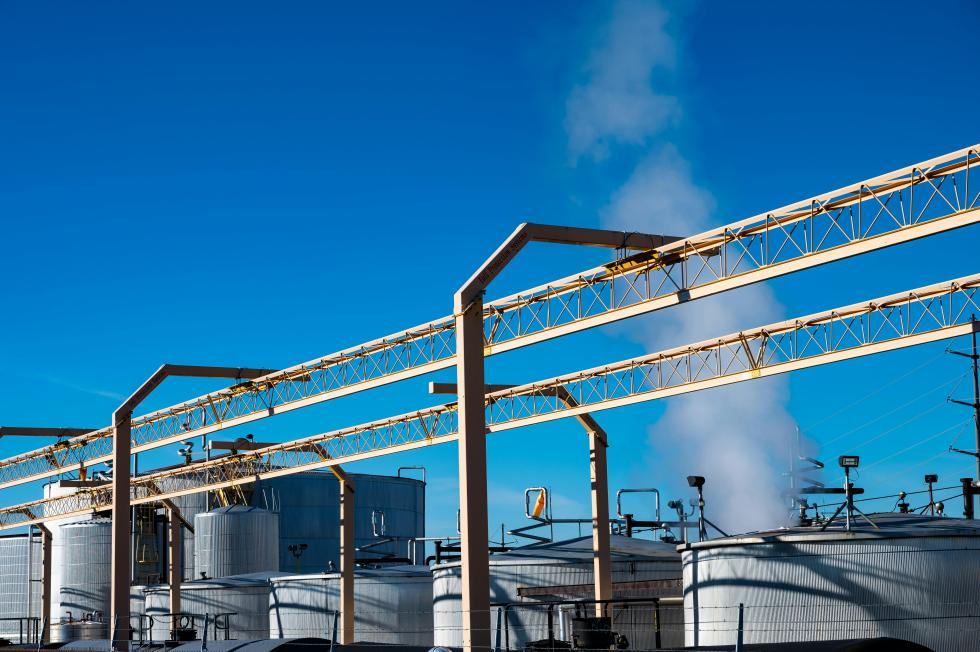
●Regular Maintenance of Emission Treatment Equipment
Rigorous preventative care takes place on emissions control apparatuses like boilers, dryers and recovery ovens to ensure optimal functionality. Fume hoods and ductwork receive comprehensive washdowns during shutdowns to remove any particulate buildup. Filters and scrubbers are replaced ahead of scheduled life cycle conclusion to safeguard performance against degradation.
Thorough logs document all inspection, testing, maintenance and calibration activities to demonstrate regulatory adherence. Proactive repairs also minimize unexpected downtime and costs from potential emissions limit exceedances. Ongoing dedication to operational excellence reflects the company’s commitment to sustainable operations and environmental stewardship.
●Strengthening Monitoring of Vehicle Exhausts
Initiatives to decrease unnecessary idle periods and optimize routes have trimmed greenhouse gas emissions from transportation needs. A fleet administration system closely tracks engine operation time and operator habits using telematics. Those exhibiting inefficient fuel use undergo evaluation and retraining as needed.
All on-site load handling equipment has transitioned to lithium battery-power to eliminate facility emissions. Plans aim to convert ten percent of ground logistics to electric power by 2025. Ongoing upgrades to the conveyance network reflect the long-term commitment to minimizing climate impact through progressively greener transportation solutions.
●Adopting Low-cost Measures to Minimize Environmental Impact
Straightforward parametric changes such as optimizing air regulation ratios in boilers decreased nitrogen oxide presence by 15%. Refinement of dryer flame characteristics subtly yet appreciably reduced carbon in flue gases.
Latest powder gathering bag coatings double service lifespan while eliminating a micron of particles formerly discharged at changeout. Raising the on-site vehicle rate restriction discourages wasteful habits. Collectively, simple solutions gradually diminish our environmental impact.
Persistent commitment to renewing infrastructure and empowering staff sustains advances in responsibly managing emissions year after year. Ongoing betterment reflects dedication to continuous performance enhancement and community stewardship.
Waste Management
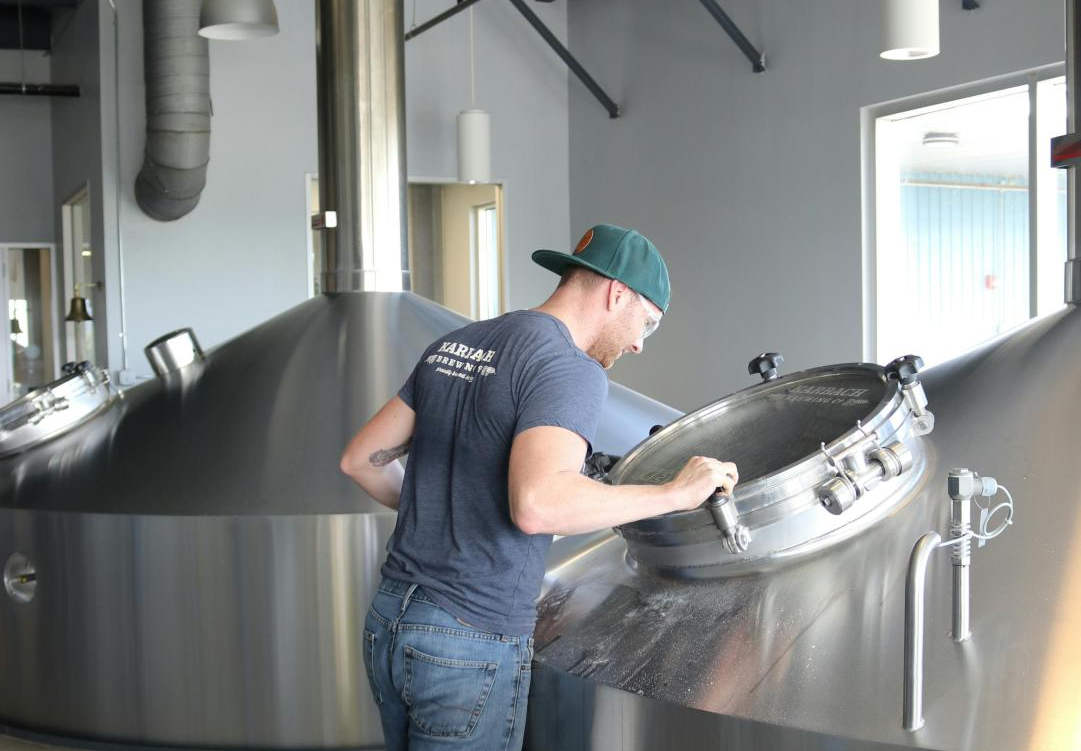
●Proper Handling and Disposal of Hazardous Waste
Hazardous residuals gathered weekly undergo rigorous documentation and conveyance protocols. On-site staff participate in yearly emergency response simulation sessions coordinated with waste handlers to facilitate prompt, lawful containment in the event of any incident. Proactive protection of environmental and community well-being remains a top priority throughdiligent waste management and constant preparedness validation.
●Recycling of Recyclable Materials and By-products
All clean paper remnants from trimming, overages and rejects undergo compaction directly to fuel combustion as a renewable resource. Diligent efforts progress optimizing manufacturing to curb such volumes.
Recyclable plastics like sleeves and dividers go through shredding and pelletizing for reprocessing. Metal components from equipment repairs are sold for remelting.
Even intricate residuals undergo examination. Pigment sediment once deposited now experiences thermal separation and smelting to release zinc oxide valued as a micronutrient fertilizer. Adaptability in disposition routes exemplifies the dedication to extracting maximum value from all outputs.
●Reducing Use of Disposable Items
Measures to reduce solid residues included phasing out one-time cups, utensils and lunch containers in favor of employee-cleanable versions. Trash minimized through limited purchases and “packaging amnesty” encouraging reuse of freight packaging.
Ongoing priorities target eliminating all single-use items while boosting recycling involvement to gain zero-waste certification. Leveraging reusable and refurbishable goods augments continuous improvement.
Prioritizing proper residue handling and maximizing material recovery sustains environmental performance through closed-loop resource stewardship. Each success strengthens productivity and lessens industrial impacts.
Fostering Environmental Awareness
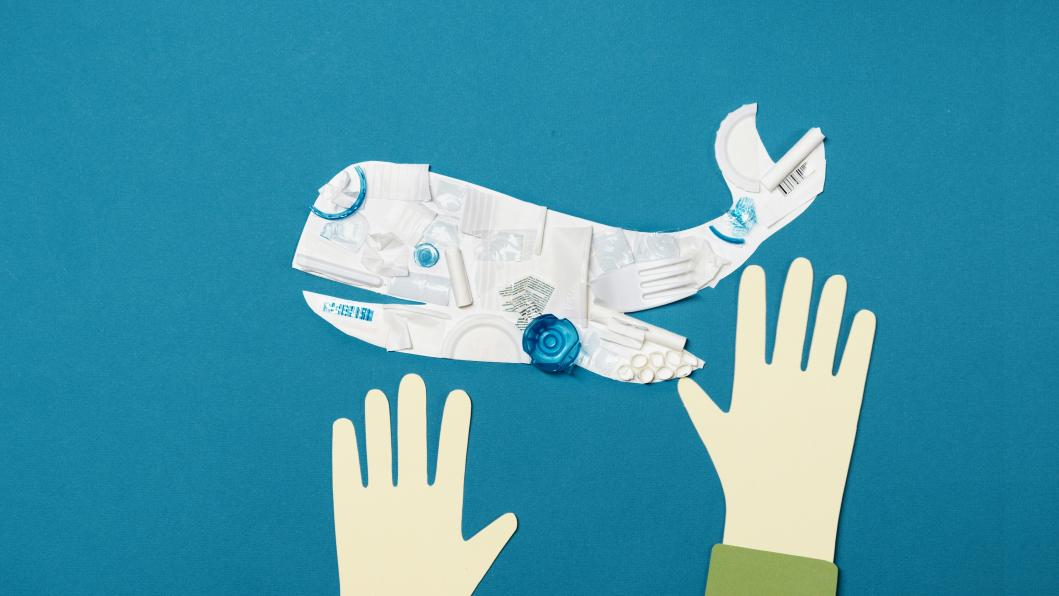
●Employee Environmental Training
New personnel complete orientation covering sustainability priorities and individual responsibilities in supporting them. Specialized job preparation reinforces protocols around curtailing energy, water and raw materials usage.
Regular seminars during lunch hours update all staff on developing initiatives for participation. Department-focused sessions explore alterations to workflows and associated obligations. A monthly electronic bulletin circulates accomplishments and best practices enterprise-wide.
Knowledge sharing through varied platforms cultivates comprehension and motivation towards continual environmental progress. Workplace culture of stewardship and engagement empowers all stakeholders in collectively advancing performance.
●Establishing an Image as a Green Factory
Signage at entries and hubs emphasizes environmental wins and targets. An exclusive online and bulletin board area features undertakings and staff involvement using triumphs and data in straightforward, everyday language.
Outreach publications highlights sustainable paper traits, core benefits and responsible manufacturing. Facility visits for providers and neighborhood spread insight into constant progress obvious enterprise-wide.
Transparency through multi-pronged communication nurtures environmental rationale and motivation. Information circulation cultivates understanding and assistance for ongoing journey towards superior outcomes. Together with dedication inside and outside, understanding grows around considerations and achievements uplifting sustainability performance.
●Soliciting Suggestions for Improvement
A eco- roundtable representing all timetables congregates consistently to audit operations for fresh competencies. An nameless suggestions container collects entries rewarded through quarterly lotteries. An once-a-year eco-enhancement challenge lures many submissions judged for practicability and savings possibility.
Since unveiling, over 75 personnel recommendations have been executed – from simple rectifications like undertaking scheduling to significant capital initiatives. Continuous two-way interaction preserves momentum for both environmental and employee well-being rewards.
Prioritizing environmental education and engagement across the workforce strengthens personalized commitment to sustainable habits as a united workplace. Continuous progress stems from collaborative problem-solving and idea-sharing at every level of operations.
Conclusion
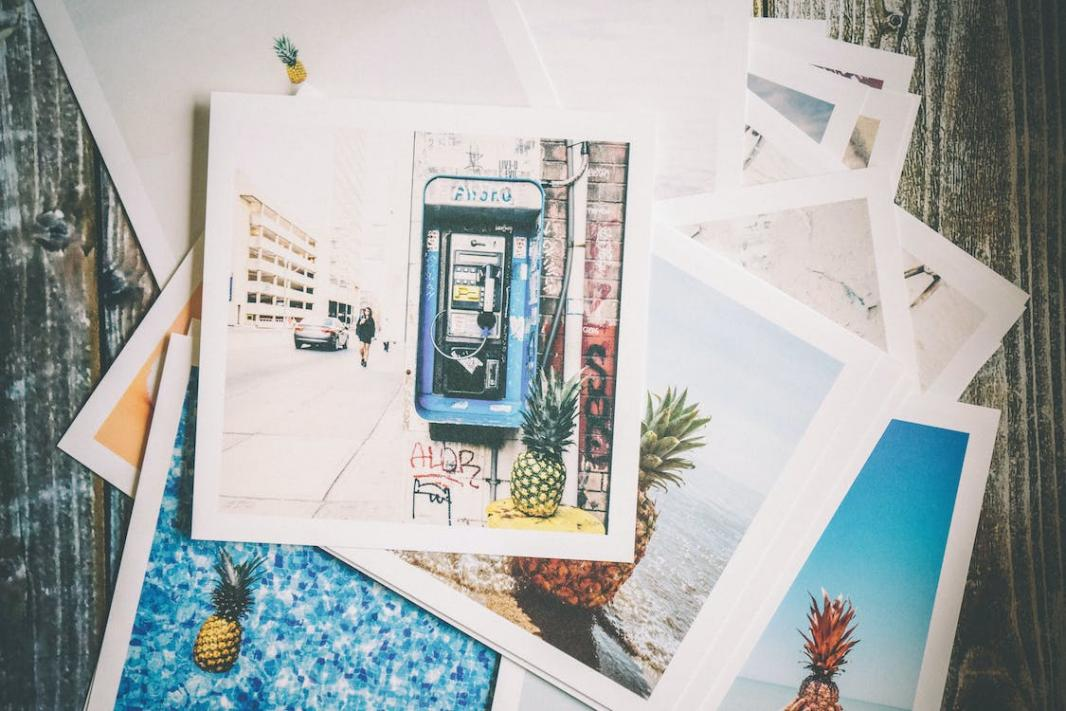
Through diligent focus on constant progression, our facility has realized significant achievements across multiple fronts of environmental output in recent years. Regular optimization of manufacturing procedures and processes has meaningfully trimmed vitality intake while water recycling now returns over 60% of application back into making.
Thoughtful material stewardship combined with electronic prototype solutions has slashed trial production’s first substance demands. Proactive appliances servicing maintains air and water emanations oversight at full proficiency. Waste diversion projects successfully recover 95% of by-products from landfilling by funneling them back internally or through end-of-life recycling.
Personnel participation through education, communication and eco-suggestion sharing nurtures a culture that increasingly considers sustainably in day-to-day duties. Externally, establishing our manufacturer’s environmental trustworthiness attracts forward-looking partners helping augment effectiveness.
Most significantly, unrelenting focus on improving resource competency through constant small steps, just as with manufacture quality, will future-proof our business from unpredictability. Continuing nimble enough to seize opportunities that develop will drive our sustainability trajectory alongside industry peers. Our facility is devoted to this prudent, long-term perspective empowering community well-being and environmental protection in tandem with responsible commercial success.