Photo labs field many inquiries from photographers about printing issues and paper choices. Common questions revolve around inventory management, preventing edge fading or curling, resolving blisters, and how paper affects quality. This article aims to address these frequently asked topics by exploring effective strategies and best practices. Readers will learn techniques for curbing moisture that causes curling and blisters. They will also discover how different paper coatings and properties influence photos. By gaining insights into standard photo paper concerns, labs can more confidently advise clients and deliver optimal solutions. Implementing these recommendations ensures consistent, high-quality output.
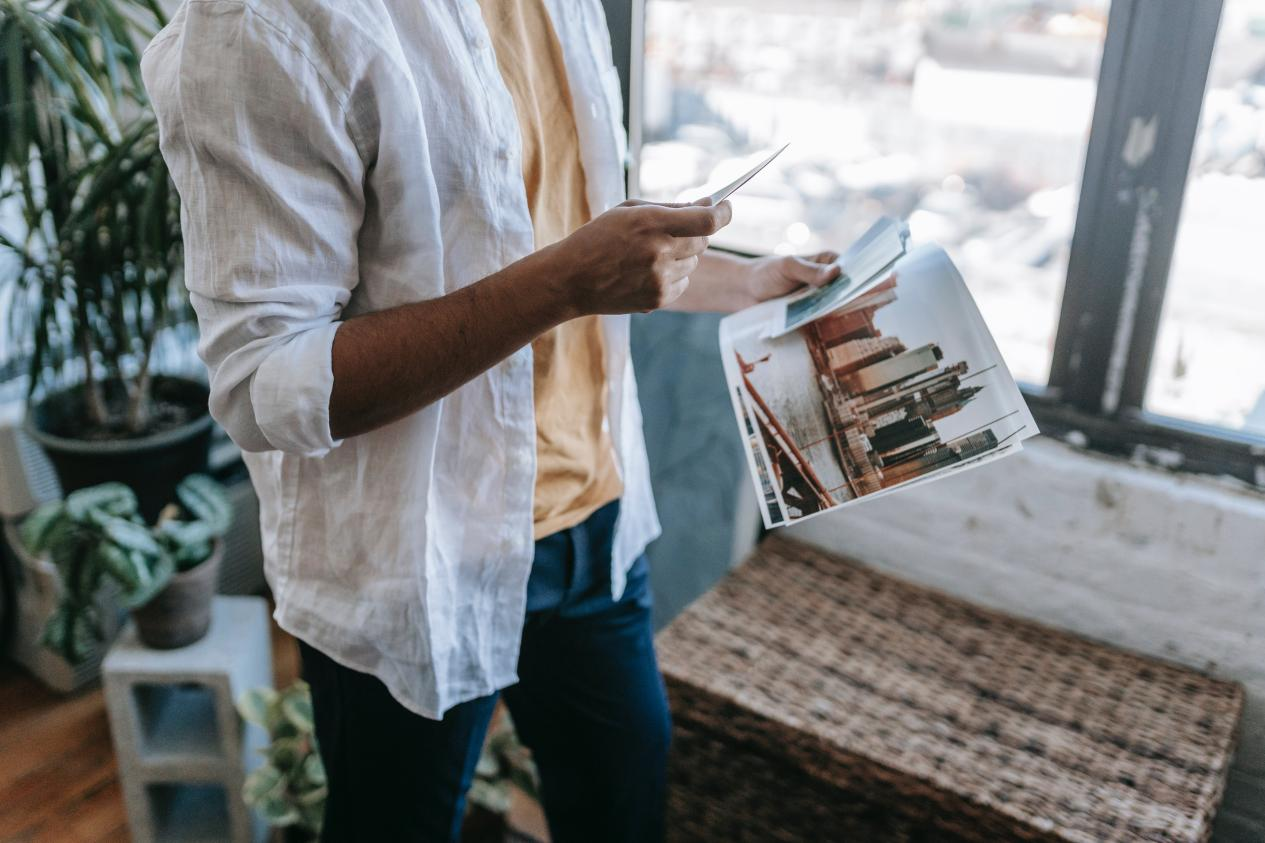
How to Effectively Manage Photo Paper Inventory?
● Predict Demand to Plan Procurement
Effective inventory management relies on accurately predicting photo paper needs. Identify trends in past sales by paper type, size and finish by analyzing records. Regular exchange with suppliers helps secure reliable stock availability. Consider upcoming events and projects that could impact demand. Optimize reordering levels and quantities to maintain adequate provisions without surplus. Evaluate procurement history to refine the replenishment process. Calibrating replenishment aligns stock to real needs. Forecasting allows timely replenishment to avoid shortages. By analyzing sales patterns and suppliers’ capacity with scheduled projects in mind, businesses can cost-effectively maintain a balanced photo paper inventory through demand-driven replenishment.
● Optimize Storage to Save Space
Effective stock handling ensures smooth customer service. Storage presents challenges with photo paper assortments, solved through organization. Boxes systematized by finish, size and quantity facilitate retrieval. Specialty papers’ convenience contrasts bulk items’ dense configuration. Wall/overhead racks elevate boxes, economizing floorspace. Regular rotation prevents aging stock expiration. Protection from moisture, dust and damage via sealed bags/boxes/shelves preserves quality.
Streamlining involves categorized sections by attribute simplifying picking. Location labeling hastens ordering and replenishment. Daily monitoring like barcode scanning precludes popular items’ lack. Physical counts periodically reconcile records with tangible stock, finding disparities. Optimization incorporates seldom-used paper’s off-site storage at a nearby third-party warehouse until needing, liberating valuable space. Right forecasting, categorization and surveillance maintain ample supply while trimming storage demands and wastage risk. Proper control undergirds smooth operations.
How to Prevent Photo Paper Curling?
●Choose Appropriate Mounting for Different Thicknesses
Lighter papers prone to curling post-printing due to moisture warpage require special mounting. For glossy or luster sheets under 250gsm, non-PVC boards like foamcore or gatorboard receive dry-applied prints through spray-mount adhesive. Heavier 300gsm+ papers endure direct taping or pinning onto rigid surfaces. Avoid stapling or dots potentially marring surfaces over time.
Extra stability becomes crucial for metallic or textured prints. A removable spray slightly bonds each between dual foamcore for flatness. Reinforce further by edging and corner-taping. Framing behind glass employs acid-free foam tape completely encircling to hold shaped prints immaculately level without stress points. Proper mounting preserves delicate media through structured, unwarping support.
● Control Temperature and Humidity Environments
Curling commonly manifests in humid conditions through moisture gradients inducing uneven drying. Particularly monitor seasonal transitions. Maintain printed photos flattened overnight at 30-50% humidity before mounting or framing to properly condition paper and prevent warping.
Similarly, temperature fluctuations impact paper as its dimensional shifts contrast surrounding materials’. Storage within climate-regulated surroundings reduces extremes’ effects. Frames permitting ventilation while distorting minimally from thermal variations suit displays.
Counteracting natural fibers-warping forces necessitates pairing suitable mounting or framing by caliber with humidity and thermal regulation. Choosing construction allowing respiration inhibits warpage from variability. Careful handling post-printing enables studios to convey flat, sharp images retaining museum-calibre quality satisfying clients. Techniques balancing the medium against humidity, temperature and deployment optimize longevity.
How to Prevent Photo Edges from Fading?
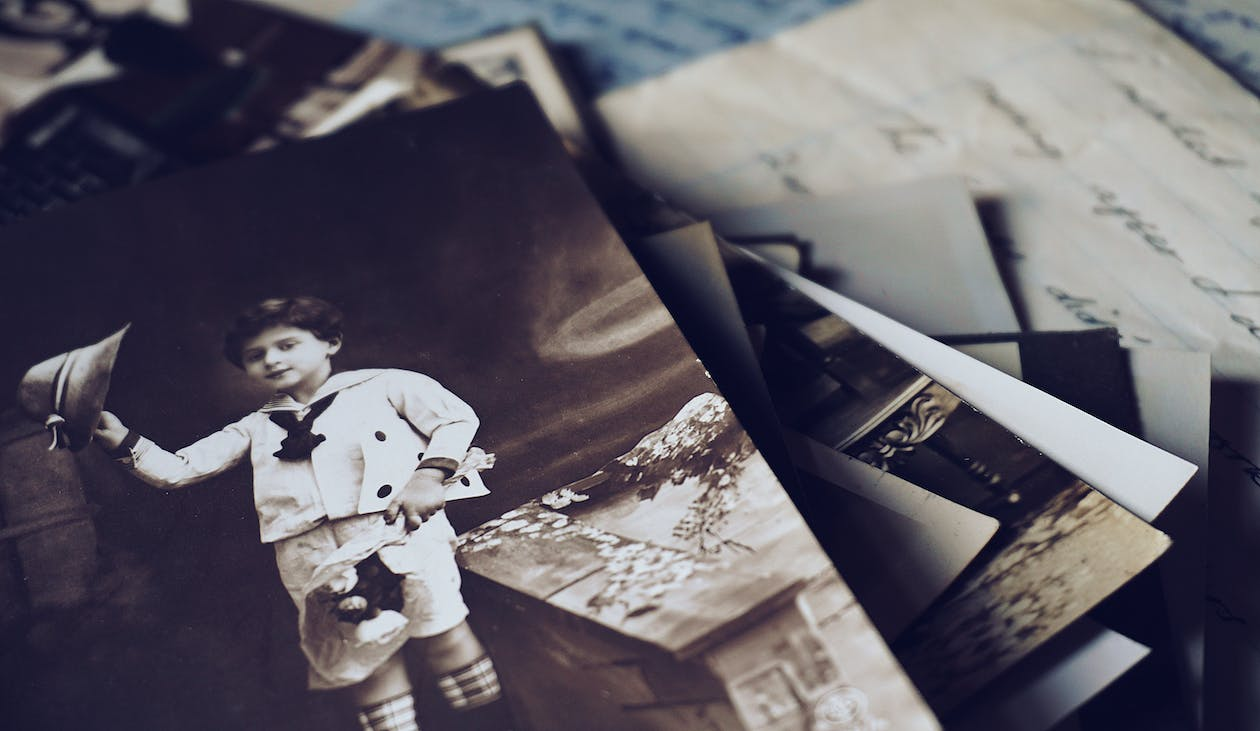
● Optimize Settings for Different Printing Methods
Inkjet print edges experience dye degradation risks from oxidation absent sealing. Enabling printer functions depositing minuscule ink droplets seamlessly marries colors to paper borders forestalls deterioration.
Thermal and dye-sublimation require divergent tactics. Tests imprint small pictures with 0.25-0.5cm outward-printing color rims shelter paperway sensitizing dyes from longterm environmental impacts. Optimal shielding margin sizing derives from test prints evaluating each stock.
Minute droplets or color perimeters preserve sensitizers over durations. Tailored safeguard dimensions originate from analyzing stocks through test imprints. Preventative measures avert damaging oxidation exposed edges undergo. Techniques shielding papers from elements sustain image vivacity. Studios adjust practices shoring up imprint permanence contrasting processes demand.
● Detailed Edge Treatment Techniques
Immediate post-processing forestalls fading for any imprinting. Softly fringe prints’ perimeters with dense graphite or micro-tip inking stylus. Blend graphite smoothly, avoiding picture areas.
As an alternate, mist edges at 12 inches with an acrylic sealer formulated for such uses. Thorough drying precedes handling sealed prints.
Mounting integrates marginal gaps between mats and borders. This sheltered “pocket” protects against abrading factors and brightness causing degradation over time. Non-UV glass incorporation and avoiding direct daylight prolonged permanence further.
Optimized settings depositing boundary droplets and cautious sealing maintains integrity. Photo studios furnish images and vividly preserved borders retaining quality for clients over decades. Refined practices shore permanence as required across processes.
Why Photo Quality Varies on Different Photo Papers?
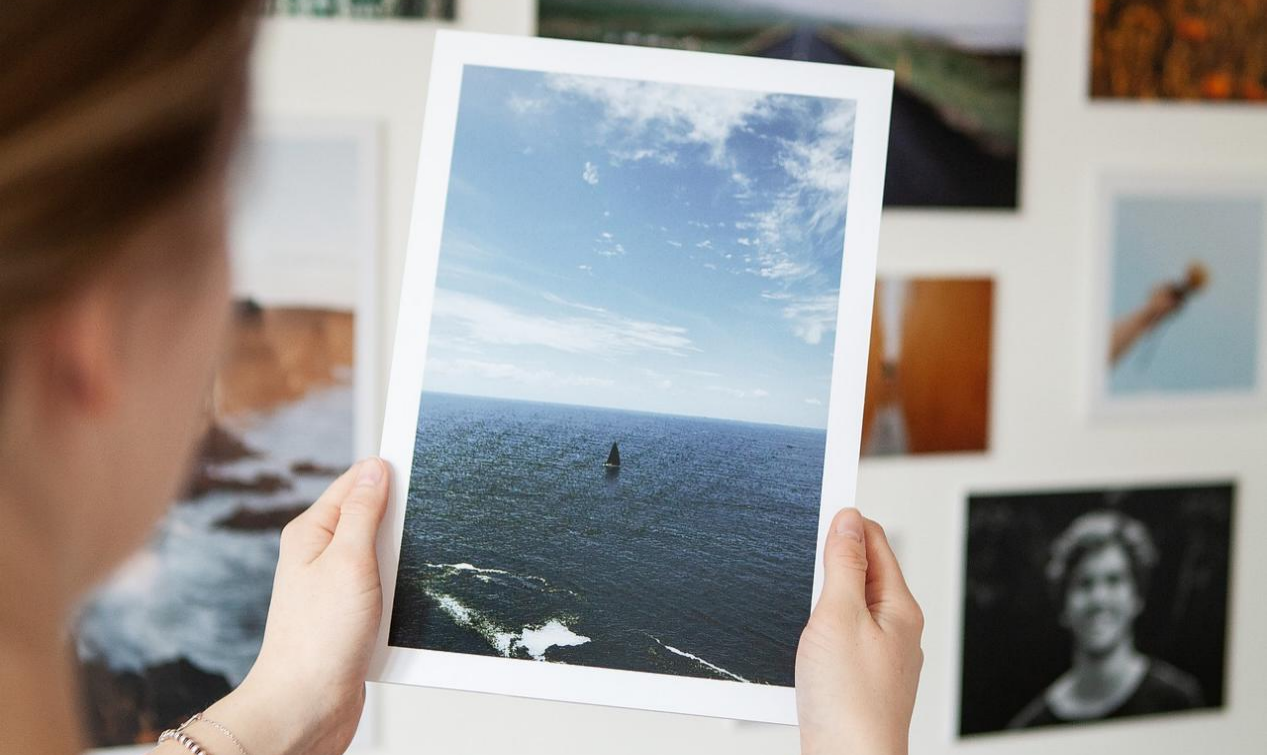
● Surface Characteristics Impact Color Rendering
Photo paper selections denote diverse substrates, coatings and textures impacting absorption and appearance. Factors to consider include brightness, weight and finish.
Glossy sheets with smooth non-porous surfaces yield sharp details and rich saturation but also spotlight flaws. Luster or pearl tones pleasantly diffuse illumination suited for portraiture maintaining clarity.
Offering lowest contrast, matte variants scatters light evenly across porous fibers albeit with reduced gamuts potentially resembling dullness against glossier options. However, heavier papers retain inks better ensuring permanence at the risk of banding or granularity with lower resolution files. Comparatively, lightweight sheets disguise deficiencies less easily.
Production aptitudes impact selections. Qualities like uniform light diffusion or resilience to printer inadequacies motivate choices coordinated to applications and intended effects.
● Match Papers to Prints for Higher Quality Rates
Leveraging paper properties necessitates considering image essence during choices. Landscapes benefit from glossy’s extensive gradations and sharp architecture while luster flatteringly renders complexions pardoning lighting variations. Metallic and specialty substrates selectively augment artistic efforts.
Test imprinted samples validating caliber precedes mass production. Ensure color profiles accurately represent each stock. Customize resolutions, processing or settings according towards substrates.
Communicating recommendations aids clients deploying works by intended placement and subject. Attention converting particular papers’ strengths optimizes visual characteristics. Display conditions equally impact suggestions.
Careful substrate pairing maximizes each output. Professionals test configurations, calibrate equipment and advise customers, refining presentations satisfying clients. Preliminary prints examine reproductions before larger runs. Meeting visual qualities necessitates this pre-production benchmarking and proficiency coordinating variable factors.
How to Resolve Common Blistering Issues in Photo Paper?
● Analyze Main Causes
Bubbles forming pockets beneath photo paper surfaces can deteriorate prints, compromising clients’ images. Two primary causes include entrapped moisture during printing and outgassing of volatiles from paper constituents over time. Wet methods expose substrates to water, permitting encapsulated humidity. Thermal coatings may liberate gases during curing getting intercepted between strata. Improper drying, high-humidity storage or fluctuations can exacerbate such issues.
Thermal laminates potentially discharge volatiles pocketed under sheets. Wet applications potentially embed moisture. Time and environmental changes may worsen such conditions. Proper techniques preclude encapsulated pockets menacing image quality. Averting moisture incorporation or volatile capture forestalls degrading bubbles compromising prints.
● Preventive Measures
Combating moisture accumulation necessitates sufficient drying adhering to manufacturer guidelines between wet printing stages. Non-aqueous substitutes like dye sublimation avoid reintroducing water where plausible.
Environmental regulation efficiently evaporates humidity absent inducing pockets. Temperature stabilization avoids solubility alterations under coatings. Flat, sealed storage in low-moisture surroundings shields from variability.
Promptly screen arrivals, quarantining flawed sheets for preprocessing prior use. Pretreat suspect batches via moderate absorption pressing between blotters extracting captured wetness otherwise forming over time bubbles. Routine checks intercept issues early.
Understanding substrate compositions and variables introducing moisture furnishes momentum over blemish avoidance and cure. Minor protections significantly minimize reprints and relationship maintenances. Drying optimization, environmental governance and pretreatments counteract typical problems.