This article provides numerous tips for optimizing photo paper inventory management, including analyzing sales data to forecast demand, considering seasonality, organizing storage, tracking stock with software, minimizing waste, reviewing metrics, and employing practices like cross-docking and vendor-managed programs.
Intro
●Why Inventory Management Matters for Photo Paper Bulk
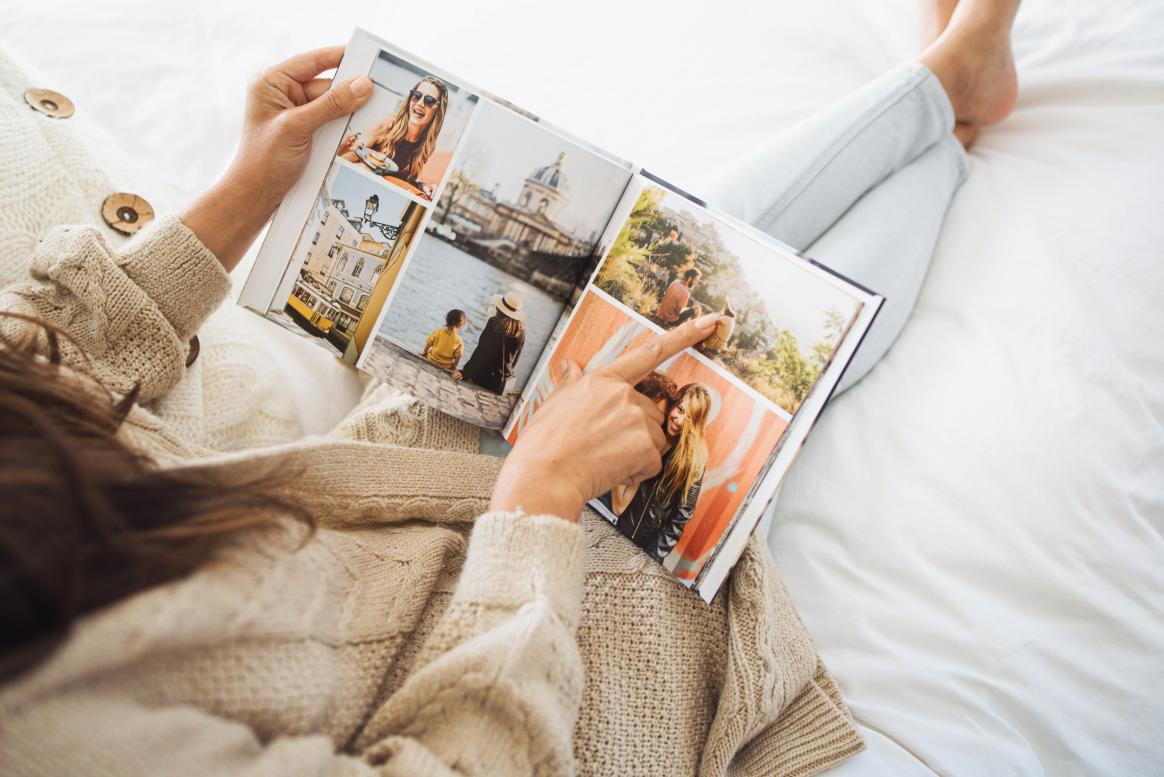
Effective inventory control of photo paper is vital for any lab, retailer or printer that stocks large quantities in bulk. With such orders come significant costs as leftover sheets can quickly expire after around 6 to 12 months. Managing thousands of different sizes, papers and brands takes proper management. Overstocks waste money if not rotated by expiration date using a first-in-first-out system. Running out is also bad, harming workflows and customers. Tight processes are needed to avoid excessive inventory levels while ensuring enough paper is accessible.
Good management has environmental perks too. The photo industry works to reduce paper usage and waste at each step. Making sure bulk supplies circulate smoothly off the shelves minimizes how much becomes trash later on. It saves resources while helping companies shrink their carbon footprint. Proper reorder levels based on actual needs helps labs and shops uphold sustainability goals as well as the bottom line. Careful inventory practices are a win-win for businesses and the planet.
●Goals of Managing Photo Paper Bulk Stock Effectively
The primary goals of implementing robust inventory processes for bulk photo paper are four-fold. Firstly, optimal management looks to minimize carrying costs by keeping stock levels of slow-selling or expiring goods low. Secondly, it helps prevent stockouts and backorders that hurt customer service. Thirdly, effective processes can reduce paper waste from goods going bad while stored. Finally, the goal is to provide real-time visibility for ordering, ensuring replenishments are done at exactly the right time, neither too soon nor too late. Achieving these aims through diligent tracking and controls leads to considerable savings over the long run through reduced costs, higher productivity and greater customer loyalty. With tight inventory practices, businesses can better serve clients’ needs while minimizing waste and containing expenses.
Planning Bulk Photo Paper Purchases
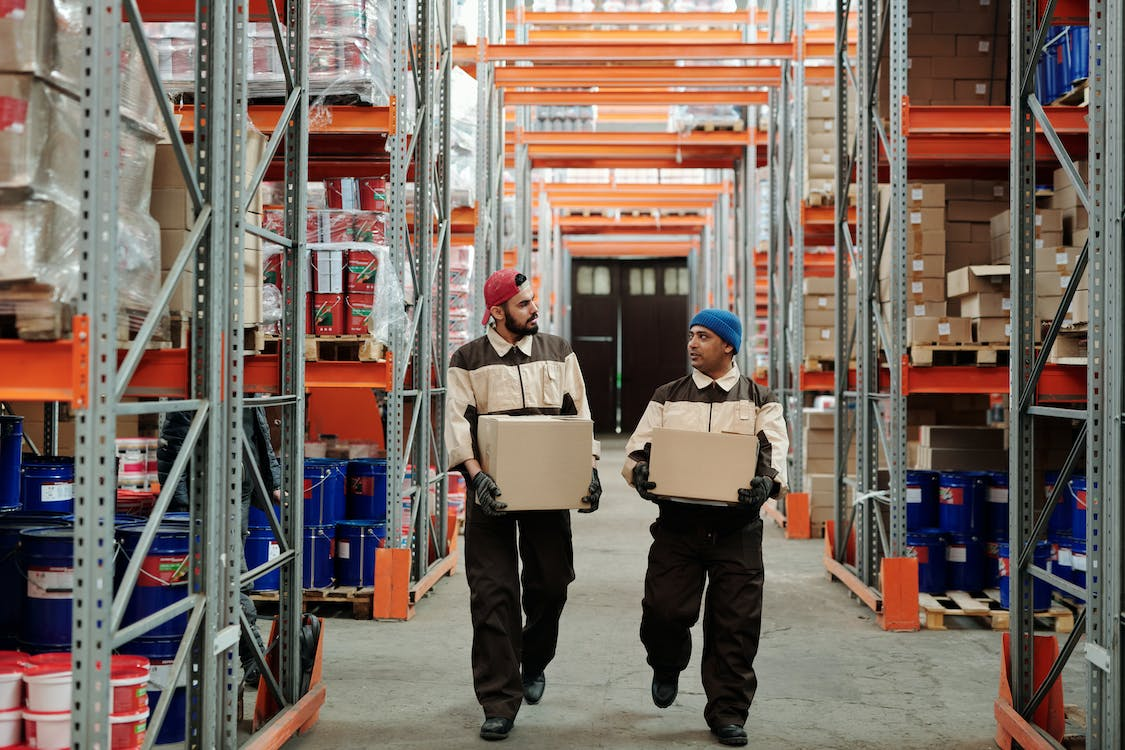
●Determining Your Store/lab’s Monthly Printing Needs
The initial step in bulk photo paper purchasing is analyzing past sales figures to determine the average monthly quantity sold of each paper type and size. Variables like print volume, consumer versus commercial orders, and new products affecting needs must be considered. It’s important to factor in any planned adjustments that could change demand. Maintaining 12 months of rolling data enables monthly demand comparisons to identify trends. With historic usage data, businesses can better project purchasing requirements based on average sales quantities segmented by paper attributes and accounting for aspects influencing demand from one period to the next. This analytical approach supports making informed bulk buying decisions tailored to a company’s specific sales patterns and market.
●Forecasting Seasonal Demand Variations
It is crucial to consider seasonal patterns when establishing a photo paper budget. Demand commonly surges around major holidays as examples. Forecasts must integrate additional periodic aspects like back-to-school seasons and seasonal retail sales that influence trends. Anticipating regular monthly swings stops companies from stocking insufficient quantities when usage spikes. It also avoids over-purchasing when volumes tend to be lower. By gauging typical fluctuations across the year, businesses can maintain stock arrangements to satisfy uneven requirements. This supports fulfilling spikes in demand during heavier periods while preventing excess inventory as needs decline. Proper allocation adjusts to changing patterns to optimize supply throughout each cycle.
●Considering Lead Times When Reordering
Lead times for bulk photo paper replenishments commonly stretch several weeks. As a result, reorder points must be established far enough ahead of anticipated consumption to facilitate timely supply. Consulting with vendors about standard and expedited delivery windows aids replenishment preparation. Accounting properly for the time required for fulfilment helps sidestep stockouts. Factoring in lead schedules ahead of projected depletion assists places replenishment requests sufficiently before inventory drops too low. This affords suppliers the lead time needed to complete orders ready for upcoming demand. With careful timing of reorders relative to expected need, stock monitoring programmes can maintain continuous availability.
●Purchasing Appropriate Bulk Quantities
With monthly demand projections and lead times incorporated, bulk order amounts can be established. Industry standards commonly suggest retaining 1-2 months’ worth of stock, although this may differ based on considerations like storage constraints or suppliers’ minimum order quantities. Consolidating orders into larger periodic shipments rather than many small frequent ones can also access volume discount pricing to balance out higher capital invested in inventory holding. Larger bulk buys taken advantage of discounts granted for increased volumes despite greater short-term inventory investment tied up. Periodic sizable transactions leave flexibility to fulfill needs for extended timeframes and offset costs through wholesale rates.
Setting Up Your Storage
●Designating A Storage Space
When setting up bulk photo paper storage, a dedicated area is important. The location should be protected from direct light, heat, and moisture variability. It requires insulation from sunlight and heat sources that can hasten expiry. Humidity level volatility should also be blocked. To determine shelving and stacking specs, account should be taken of maximum predicted inventory. Adequate ventilation is further required. By designating a suitable, isolated region apart from perilous environmental factors, stock can maintain freshness for its recommended lifespan. Sizing the storage locale based on peak predicted volumes ensures fitting capacity to avoid overcrowding that risks compromising quality. Proper conditions extend usability timeframes.
●Organizing by Paper Type/size/brand
Organizing the inventory systematically facilitates easier auditing, counting and distribution. Cluster goods together based on pertinent distinguishing factors such as paper surface type, size or manufacturer brand. Clearly mark the areas and shelves so products can be easily found. Implement controlled rotation of supplies using bins, boxes or coverings clearly labeled with enclosed contents. Group similar items near one another and identify locales unambiguously to streamline stock management procedures. Regularly designating new goods to the front maintains FIFO protocols and avoids expired paper residing undistributed for lengthy time periods.
●Using Shelves, Pallets, Bins Appropriately
To optimize space usage within the storage area, shelves and containers should be efficiently utilized. Heavier boxes brimming with 8×10 photo paper and larger sizes benefit from ground-level placement, potentially consolidated on pallets too for easier handling. Lighter paper packs or compact configurations are better situated at higher heights. Dividers segregate dissimilar stock keeping units. Strategic vertical and horizontal allocation based on weight classes minimizes handling hassles. Lower positions accommodate bulkier, more burdensome goods while higher shelves suit lighter, smaller loads. Dividers offer organization of merged assortments. Systematic arranging extracts fullest value from available storage real estate.
●Arranging for First-in, First-out Handling
Adhering to FIFO (first-in, first-out) principles means placing new bulk paper shipments behind current stock so older items are used before more recent deliveries. Date all incoming bulk paper shipments upon warehousing to transparently recognize the sequence of stored goods. This permits discerning what was placed in inventory storage initially to avoid mistakenly selecting more recently received supplies first when replenishing. With clear identification and systematic rotation of goods, expired paper resides on shelves for minimal periods. Proper stock rotation supported by clear receipt dates extends usable lifetimes. Complying with FIFO safeguards diminishes waste and maximizes value retrieval from inventory investments.
Tracking Your Inventory
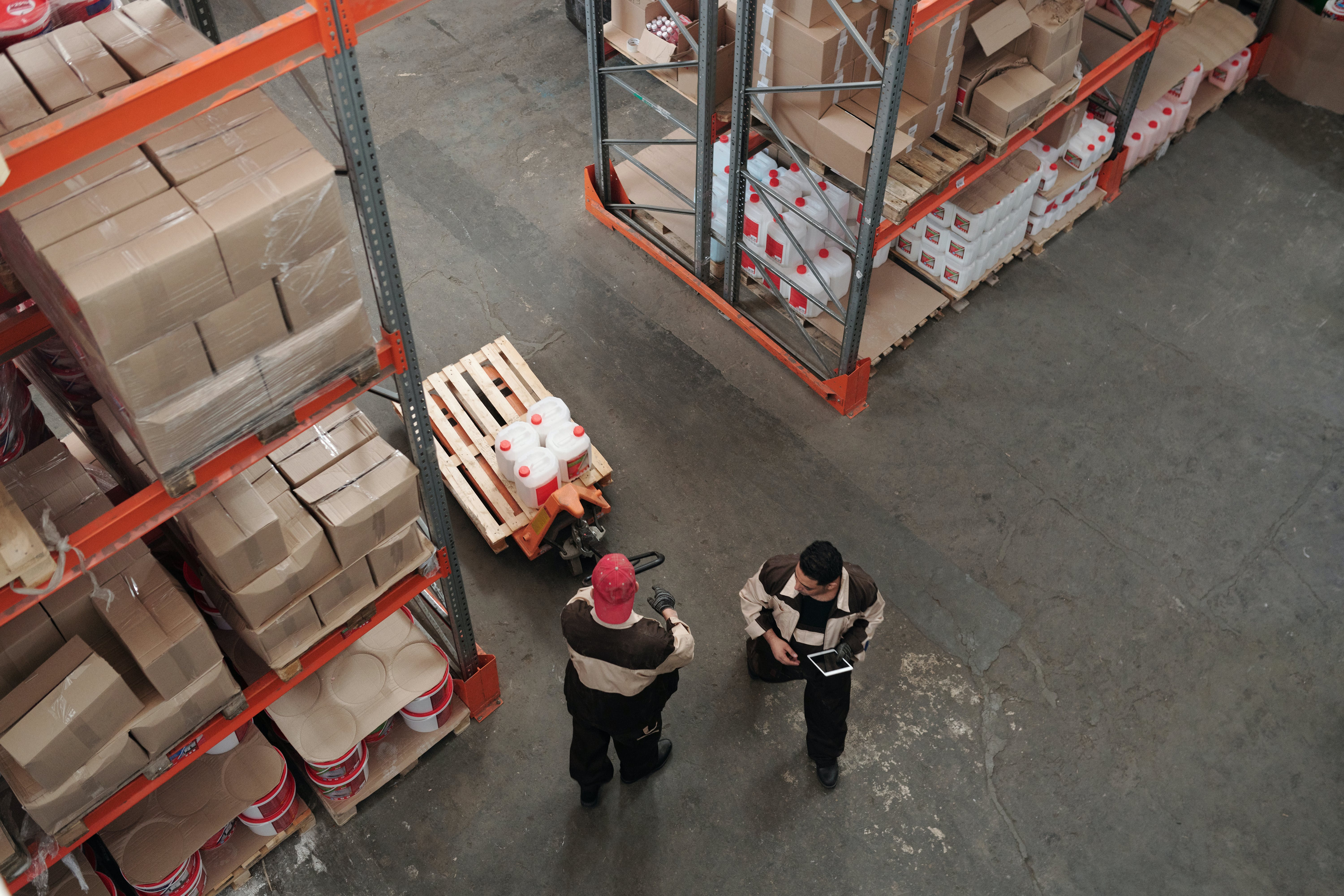
●Choosing Inventory Management Software
Technology can streamline paper tracking through tailored business software. Features like barcode scanning, mobile access, automatic reorders based on usage, and reporting capabilities are advantageous. Integrations with accounting programs automate financial aspects as well. Evaluate options scaled appropriately from free or open-source to robust paid solutions. Simplified monitoring is attainable through programmable inventory management designs. Key elements include ordering tie-ins, usage trackers, and customizable dashboards. Compatibility with other systems streamlines finances. Customizable to company scale, software automates processes for improved control and insight across storage, movement, and expenditure of stock.
●Setting Par Levels for Reordering
Establish minimum and maximum inventory thresholds to automatically trigger replenishment, such as minimum par levels and ceilings like 1-2 months of stock. Consider delivery timeframes and unpredictable usage patterns when setting these values. Initially implement conservative thresholds, then analyze multiple reorder cycles before adjusting as needed based on actual consumption rates. Minimums initiate orders to restore stock while ceilings prevent excess. By cautiously pilot testing inventory parameters upfront with prudent starting limits, experience over subsequent rounds of replenishment provides hard data to inform tweaks ensuring stable supply without overstocking. Adjustments delivered continuous improvement in forecast accuracy.
●Conducting Regular Cycle Counts
Routine counts uphold precision, pinpointing inconsistencies in advance. Schedule them monthly especially post-peak periods. Biannual full physical stocktaking of storage facilities occur along with quarterly random checking of faster-turning items. Printing reports for audit trails notes variances. Notations update holdings to actual levels and revisions such as order fulfillment status. Regular counting at set frequencies like monthly after high-traffic seasons and twice-yearly comprehensive inventories maintain exact visibility. Unannounced quarterly spot checks on swift movers further validate quantities listed. Discrepancies receive quick remedy through amended records budgeted accurate supply.
●Recording Usage Data Over Time
Detail paper amounts on each order, sale and project, recording size, surface and quantity. Periodically analyze type and volume trends over time to recalibrate projections and allotments. Identify shifts including reorder frequencies or seasonal patterns, flagging usage increases/decreases exceeding 10% for follow-up. Develop seasonal adjustments when helpful. Regularly collecting supply levels, transactions and depletion information through automated checks and physical audits delivers ongoing visibility into demand patterns. This ensures having suitable paper amounts available while preventing overstock through continually refining expectations in line with actual consumption changes and special times of higher/lower needs. The consistent tracking loop maintains balanced inventory suitable to requirements without surpluses.
Improving Inventory Forecasts
●Analyzing Past Order Patterns
Assess past order records to ascertain frequently procured paper varieties, dimensions and amounts on a monthly basis. Recognize patterns such as augmented softcover textbook manufacturing in autumn seasons. Developing projections grounded in multiple precedent years of procurment chronicles if obtainable better readies for variabilities from year to year. Scrutinizing former procurement narratives illuminates repeatedly stocked paper styles, sizes and quantities by month to month to champion accuracy when anticipating forthcoming needs by season. Long-term data analysis facilitates scheduling assured inventory in keeping with cyclical or developing procural customs above short-term outlooks alone. Prognoses informed by diverse prior yearly procurement histories enhance stability of inventory kept according to practical expectations.
●Factoring in New Product Lines/services
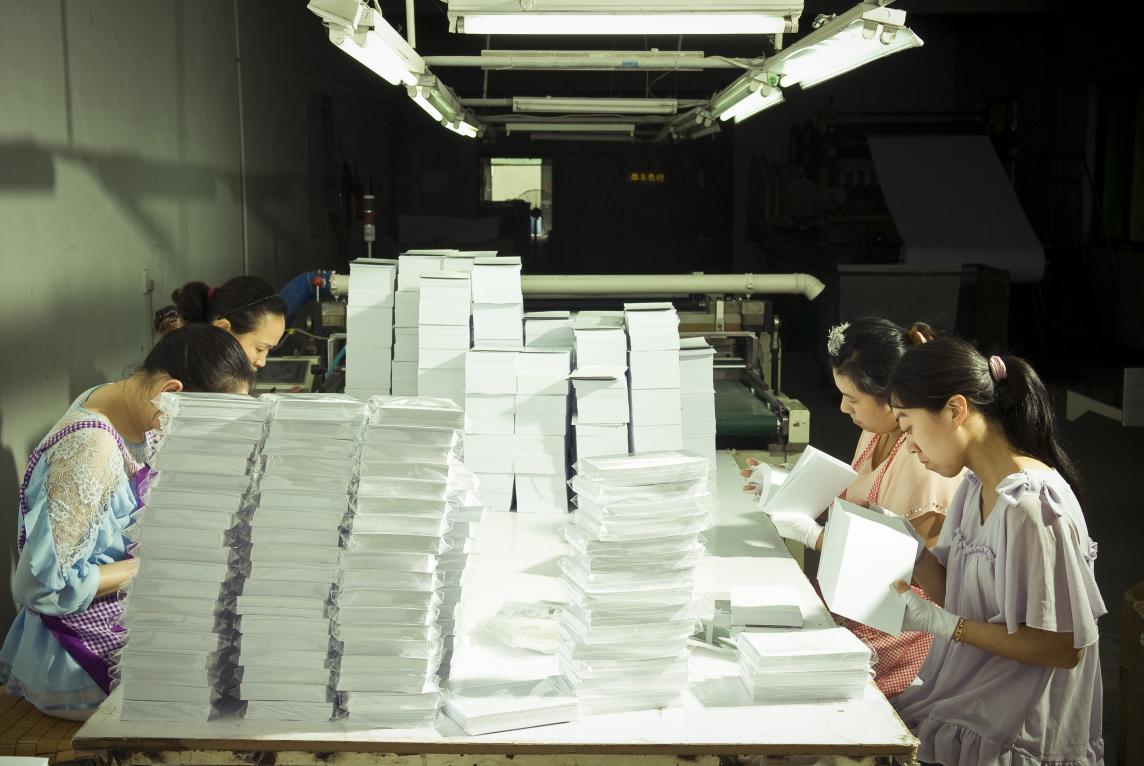
Anticipating needs involves accounting for potential paper type/size alterations from new product/service additions. Examples include extra 4×6 sheet needs when launching passport photograph services. Substrate desire changes with lab machinery upgrades also influence projections. Pilot hypothetical product/market tests provide demand impacts insights. Forecasting examines how prospective offerings like enlarged passport photos might impact particular paper category request patterns prior to scale launches. Estimations incorporate paper variances anticipated from testing hypothetical service/gear developments. Careful modeling of supplementary product/equipment effect on procurement habits enhances inventory’s responsiveness to emerging requirements.
●Adjusting for Changes in Sales/operations
Strategies, teams and market dynamics facing change over time necessitate adjustment. Compare quarterly earnings year-over-year to pinpoint categories declining or exceeding usual rates aiding refinements. Observe novel customer wins or losses and production divergences from standards necessitating recalibration. Consider deviations for anticipated shop closures, renovations or seasonal holidays when predetermining requirements. Accountability toward shifting circumstances strengthens provisioning. Annual quarterly profit reviews versus past benchmarks detect weakening or intensifying demand types and revenue streams helping modification. Deviating customer, output or planned shutdown account changes require factoring for continued precision.
●Updating Forecasts Quarterly
Set aside dedicated time each quarter for prognosis refinements. Factor yearly monthly earnings changes, prevailing inventory levels and adjusted quarters incorporating latest seasonal patterns, special deals impacts, provider lead periods with irregular unforeseen variances flagged. Record rationale and acquire approvals guiding successive financial intention. Models iterate alongside emerging real data. Frequent appraisals encompassing all external issues deliver most exact projections for bulk requisitions confirming inventory stays streamlined yet dependably backing printing needs. By systematically studying year-over-year earnings modifications, current holdings alongside unforeseen issues each quarter coupled with latest information, estimations progressively near optimal precision ensuring demand fulfillment without oversupply.
Minimizing Waste and Spoilage
●Checking Expiration Dates upon Receipt
Photo paper typically reaches end of shelf life within 6-12 months post manufacture. Make note of delivery dates to enable expiration period determinations identifying soonest and latest expiry. Inventory storage receives strategic organization together as per expiry cycles with products nearing end of usability foremost for first deployment. By factoring the typical utilization phase measured from manufacture timing and keeping closer dated products most accessible, output needs receive satisfied while minimizing waste from expired paper. Sequencing stock reliant on remaining viable timeframes optimizes value extraction from holdings.
●Rotating Stock Using FIFO Practices
Consistently selecting earliest shipped stock first ensures consumption within viability timelines. Date all incoming product batches and routinely audit warehouse situations checking this protocol, refining where necessary. This earliest expiry/first use (FEFO) approach maximizes time frames for safe applications, thinning waste potential. Regularly confirming the stock selection system removes oldest initially via periodic storage checkups guards against any protocol deviations ensuring paper and chemical items retain effectiveness for needs as longevity extends through disciplined first-in, first-out issuance tied to received dates. Adapting processes as periodic reviews expose gaps protects against spoilage while fulfilling output requirements.
●Ordering Sufficient Quantities
Excess inventory weakens cash flow and results in wastage should holdings expire before usage. Yet maintaining too little creates stockout vulnerability. Striking a balance is advised – keep recommended 1-2 months cover according to projections to guarantee all papers circulate prior to end dates. Neither over-supplying nor under-supplying serves business needs. The optimal strategy sees inventory equal to forecast 1-2 month consumption to avoid potential cash drain and utility loss from surpluses exceeding shelf life, while reducing out-of-stock risks compared to maintaining low safety levels alone. Judicious provisioning at recommended cover level by anticipated utilisation maintains viability of holdings and service ability.
●Donating/returning Unused Surplus
Inevitably, remnants surface nearing termination dates regardless best practices. Request credit or alternatively disburse unopened paper to charitable visual arts initiatives and educational facilities for damage control, retrieving worth instead of wasted paper ending in landfill no longer fit for service. Periodic checks of dates coupled with consistent first-expiry, first-use rotation and prudent bulk requisition sizing uphold maximum practical lifespans for consignments. This retains earnings through limiting surfeited stocks neither benefiting clients nor business. Even with diligent stock administration, remnants occur; productive alternatives repurposing such inventories benefit communities while restricting negative impacts to margins from expired holdings and optimize sustainability by diverting still viable paper from disposal.
Reviewing Inventory Metrics
●Days of Supply on Hand
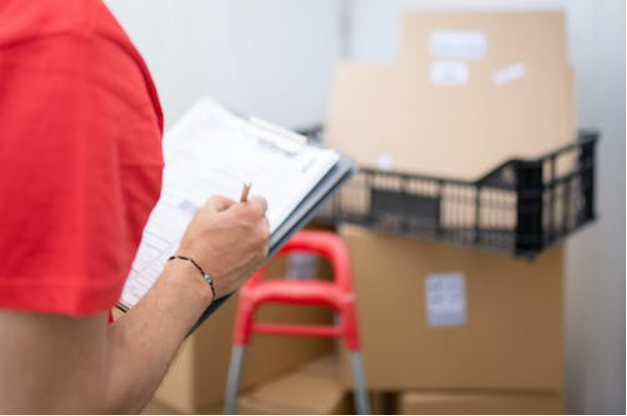
Known as stock on hand over daily consumption, this metric calculates the period holdings might sustain needs absent reordering. Across sectors, 60-90 days remains normal whereas longer immobilizes funds and elevates spoilage possibility. Maintaining inventory to satisfy 60-90 future days consumption balances cash optimization and depletion avoidance. Determined by present volume divided by daily outflow, the timeframe inventory suffices under usual depletion cautions capital allocation aligning with industry practices. Too extensive holdings demand financing exceeding sector standards with amplified wastage potential conversely too limited stock risks breaking supply chains. Calibrating procurement to support typical 60-90 day operations via this calculation optimizes working capital commitment and stock preservation.
●Stockouts and Overstocks
Tracking stockouts and expired inventory not sold annually by dollar cost averaging provides insights. High figures signal issues with demand forecasting necessitating adjustments. Monitoring and tallying yearly expenditures on out-of-stock instances or products expiring unsold aids pinpointing prognostic inaccuracies. Where prognosis requires refinement, these metrics will reflect sizeable amounts. Notable values in documenting yearly stock depletion events and held inventory surpassing best-before dates without sales draw attention to areas necessitating forecast modeling revisions. Quantifying such misses financially on an annual basis helps evaluate predictive precision.
●Inventory Turnover Rate
This metric derived from cost of goods divided by average inventory investment compares yearly sales to stock levels. Higher turnover is preferable, targeting 4-6 rotations meaning total inventory sells 1-2 times annually. It is optimal to sell full stock 1-2 times a year, indicating efficiency through rapid inventory movement. Calculating the times total inventory is sold within a year via sales divided by average holdings demonstrates working capital performance, favoring higher turnover figures around 4-6 rotations reflecting inventory sells 1-2 times twelve months.
●Dollar and Quantity Variances
Review discrepancies between physical counts and system records for values and units monthly. Identifying probable causes like input errors or cycle counting flaws. Resolving gaps beyond tolerance supports precision. Quarters see comparisons against metrics such as turnover rates revealing program enhancements. Developing issues for paper varieties or vendors become clear necessitating prompt responses preserving profits. Regular evaluations gauge key goals progress while flagging troubles regarding stock provisions, aiding decisions reinforcing earnings. Objective views arise from reports referencing important targets as program maturation delivers comprehending of stock policies maximizing funds over time.
Further Optimization Strategies
●Cross-docking between Locations
For enterprises with several sites, cross-docking means dispatching orders between branches bypassing central storage, downsizing holdings. Guarantee stock transfers among sites based on agreed replenishment points and delivery schedules to fulfill needs. With multi-location operations, direct shipping between stores from manufacturer eliminating warehousing trims stock levels on hand. Cross-site paper movements aligned with agreed depletion guidelines and mutually approved timeframes to supply each location optimizes inventory spanning distributed operations.
●Just-in-time Inventory Techniques
JIT procurement aspires to secure inventory precisely as needed to make or deliver client orders. For photographic paper, it involves reordering at minimum stock points ensuring timely receipt of latest papers ever accessible. Building close relationships with suppliers means reliable replenishment of most up-to-date paper varieties attaining JIT objectives as manufacturing/shipments require. The goal is receiving stock precisely when required to produce or fulfill, relying on trusted trade connections to replenish photo paper once minimum amounts reached, habitually keeping the newest available.
●Vendor-managed Inventory Programs
Certain major clients practice VMI involving particular stocks vendor-held on premises. Suppliers oversee quantities, trigger reorder based on algorithms. This shifts procurement responsibility and risk to business partners for specific fast-moving lines monitored and replenished by merchants at client site. With VMI, suppliers retain title of designated products stocked on-site while automatizing replenishment. Vendors manage those reservePaper lines as agreed, streamlining procurement through relieved oversight and improved availability for large organizations.
●Consignment Options for Large Buyers
Photographic paper producers may retain volume inventory at customer premises in essence on loan, billing solely as stock usage occurs. This exempts upfront capital for selective major clients preserving safety volumes accessible via web platforms. Adopting alike practices refines standard warehousing while further boosting procedures, expense oversight and area utilization for high performing print functions once principles established. Steady evaluations of latest techniques sustain competitive benefits as manufacturers and consumer reimagine traditional stockpiling architectures together progressing performance over time through innovation.
Conclusion
Managing bulk photographic paper inventory carefully matters greatly for photo retailers and print firms. It ensures reliable high quality supply while minimizing overstock and costs. As photo paper features expiration dates and represents substantial expenses, tight controls over stock prove crucial.
Numerous approaches were proposed involving needs assessment, seasonality planning, suitable inventory levels, continual improvement. Planning purchases, storage setup, stock tracking, forecasting upgrades, waste reduction and metric reviews help maintain low carrying fees and avoid shortages.
Habitual counts, analyzing usage, replenishment point changes forestall disposed cache. Cross-docking between areas and periodic projection re-evaluation plus first expiry first usage also optimize paper application. Major clients benefit from vendor administered and consignment models boosting efficiency.
Overall focus on stock management yields large financial benefits and improved client satisfaction. Implementing basic recommendations allows photo retailers to streamline bulk paper supply chains and operations for amplified profits and sustainability in the years ahead. Appropriate inventory levelling and replenishment proves pivotal to success.