Providing solutions and best practices for dealing with each problem area is the focus of this article. Ensuring labels remain prime throughout distribution, warehousing and the entire shelf life of products is the goal.
Introduction
The proper storage and handling of labels is crucial to ensure they maintain their quality from production to the point of application on products. Small issues that arise during storage can compromise the performance of labels and even lead to usability problems. As labels are a critical part of the packaging and branding of many supplied goods, their longevity has important implications for supply chain management and delivery of products to consumers.
This article discusses three common challenges that labels may encounter during storage periods. By understanding these issues and implementing appropriate preventative measures, label printers and manufacturers can secure the integrity of their labeling materials over the long term. The three main challenges that will be examined include shrinking of paper backing materials, excess adhesive bleed caused by unstable storage conditions, and discoloration of thermal adhesives from light exposure over time.
Challenge 1: Shrinking of Paper Backing
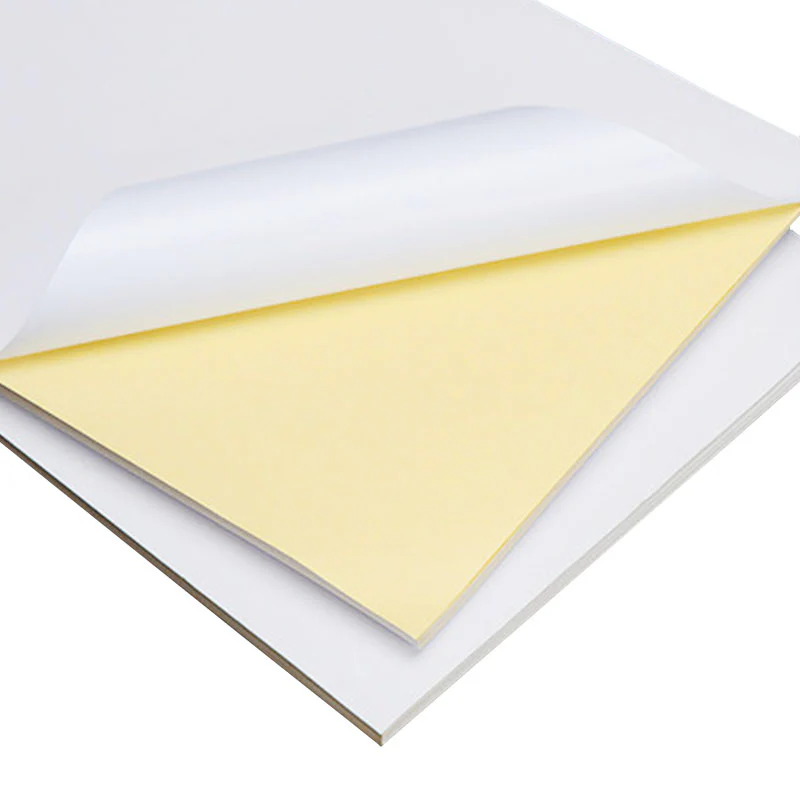
● Causes of paper shrinking due to temperature/humidity changes
The storage environment can have a significant effect on the dimensional stability of paper over time. Paper is extremely sensitive to fluctuations in temperature and humidity levels. When the temperature increases, paper absorbs moisture from the air, causing the fibers to swell. Conversely, as temperatures drop, the moisture content decreases as water is released from the paper. These subtle changes in the moisture level within the paper fibers in response to varying environmental conditions can lead to shrinkage or expansion of the material. Exposure to high heat during storage or transportation likewise increases the risk of moisture loss from the paper and shrinkage occurring as a result.
● Resulting problems like label misalignment
One of the primary issues caused by paper backing shrinkage is misalignment of the printed label graphics. Because paper contracts under low humidity, the overall dimensions of the label are reduced compared to when it was originally produced. This can pull the label graphics out of registration, distorting the intended placement and design. Another potential problem is edge lifting, where the outermost edges of the label peel up from the package or product due to shrinkage stress on the adhesive bond lines. Both misalignment and edge lifting can significantly impact the appearance and quality of labeled items.
Solution: Use papers with higher weather resistance
Koalapaper have developed formulations that are able to maintain greater dimensional stability over fluctuations in temperature and moisture. These weather resistant papers resist contractions through enhanced fiber properties that prevent warping and binding of the sheet structure even when modest water is lost.
Solution: Control backing composition
Precisely tailoring the composition of paper during its manufacturing process can boost resistance to shrinkage. Variables like the ratio and treatments of cellulose and other plant fibers impact how the paper structure responds to moisture shifts. Tighter quality control in papermaking lends greater dimensional reliability.
Solution: Store in moisture-barrier bags
Sealing labels within multi-layer barrier bags immediately after production helps protect them from absorbing or releasing moisture during warehousing and transport. This buffering environment prevents conditions conducive to paper shrinkage from exposure.
Challenge 2: Excess Adhesive Bleed
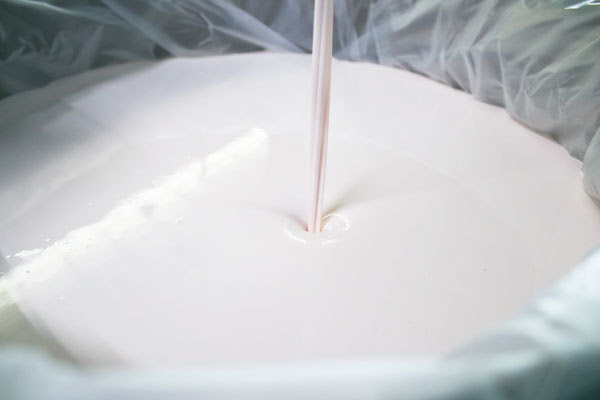
● Cause of bleed being too much glue applied during labeling
Precise control over adhesive deposition is critical to prevent bleed issues. Applying more glue than necessary during labeling can potentially lead to bleed over time as the adhesive breaks down under heat and pressure stresses. Even a small excess in glue volume dispensed may not immediately manifest as bleed but can emerge later if labels are not stored properly. Maintaining consistent glue control can help ensure labeling takes place within specifications.
● Problems such as adhesive seeping over time
When too much adhesive is present, there is an increased likelihood of it breaking through any surface barriers over prolonged storage and distribution. Excess glue may come loose from the application area and creep outward, marring the label appearance and potentially the product or package. Bleed leads to smearing, loss of print quality, and non-uniform labeling effects. It renders the labels unusable or in need of relabeling.
Solution: Carefully monitor glue volumes
Consistently confirming that glue dispensing volumes fall within the prescribed technical guidelines is important. Regular checks and adjustments to applicator calibration help avoid excess adhesive.
Solution: Koalapaper’s labels undergo QC to prevent bleed issues
Through multi-point inspection and storage testing under various conditions such as heat, Koalapaper ensures its labels withstand storage and transport without bleed. Strict quality control maintains consistent gluability free of bleed potential.
Challenge 3: Hot Melt Adhesive Discoloration
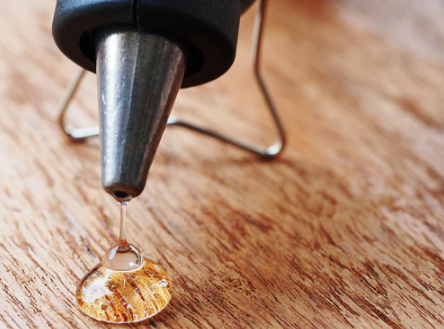
● Cause of discoloration being extended light exposure
Many labels utilize heat-activated adhesive systems that are sensitive to degradation from ultraviolet radiation and visible light exposure over lengthy periods. Stored labels confront a cumulative risk factor from unprotected lighting in warehouses or during displays and sales. The adhesives can undergo photo-oxidation, a process through which their molecular structure is damaged by light energy, often resulting in discoloration.
● Issue of adhesives yellowing and darkening over time
The main consequence of photolytic breakdown is a gradual shift in the adhesive’s appearance as it yellows or darkens with increasing light exposure hours. This visual change can detract from the aesthetics of labeled products and reduce consumer appeal over the lifespan. In more extreme cases, adhesive discoloration may compromise the bond integrity.
Solution: Koalapaper’s Advanced Hot Melt Adhesives
To address the challenge of thermal adhesive discoloration over long storage periods, Koalapaper has invested heavily in research and development of next-generation hot melt technologies. Through our own adhesive production facilities, we have formulated advanced hot melt compositions that exhibit vastly improved lightfastness compared to conventional thermoplastic formulations.
While our specially designed lightfast adhesives have a higher per unit cost of production, extensive durability testing has confirmed their ability to prevent yellowing and maintain a like-new appearance even after thousands of hours of UV exposure. This delivers tangible benefits to our customers by ensuring labeled products on shelves or in warehouses retain their intended branding presentation throughout projected shelf lives and inventory durations.
Koalapaper’s proprietary lightfast hot melts provide our global clients with a reliable solution for applications where extended light exposure may compromise typical adhesive systems. Backed by our adhesive experts and stringent quality procedures, label converters and manufacturers can trust our adhesives to safeguard their reputation for quality through years of distribution and storage.
Conclusion
Maintaining the intended quality, performance and visual appeal of labels throughout their usage period from production to consumer has always been a top priority for Koalapaper as a label manufacturer and brand owner. However, realizing this goal requires a diligent understanding of potential issues labels may face during interim storage and handling. As discussed in this article, labels are susceptible to dimensional changes from environmental fluctuations, adhesive degradation from excessive amounts or light exposure, and other stressors under uncontrolled storage. Taking proactive measures to mitigate known hazards can effectively preserve labeling materials’ integrity in the long run.
At Koalapaper, we are committed to safeguarding label integrity through actively implementing preventative solutions to the common challenges addressed, such as paper backing shrinkage due to temperature and humidity variances or discoloration of thermal adhesives from photo-oxidation. Whether specifying paper compositions better tailored for distribution conditions or enforcing strict quality control over adhesive volumes from the early planning stages, addressing root causes is advantageous.
We also provide customized guidance taking into account different product types and supply chain environments, with recommendations on label selection, material optimization and storage best practices. This assists labels in fulfilling their use purpose within projected lifecycles. We welcome all industry clients to consult Koalapaper regarding their specific labeling needs as we work together towards quality labeling solutions.