The direct to film (DTF) printing method has seen considerable growth over recent times. A vital element integral to DTF printing is the specialized powder used. This article aims to uncover the important differences between DTF black and white powders through examining their properties, suitable uses, and ensuing print outcomes.
DTF Black Powder
● What is DTF Black Powder?
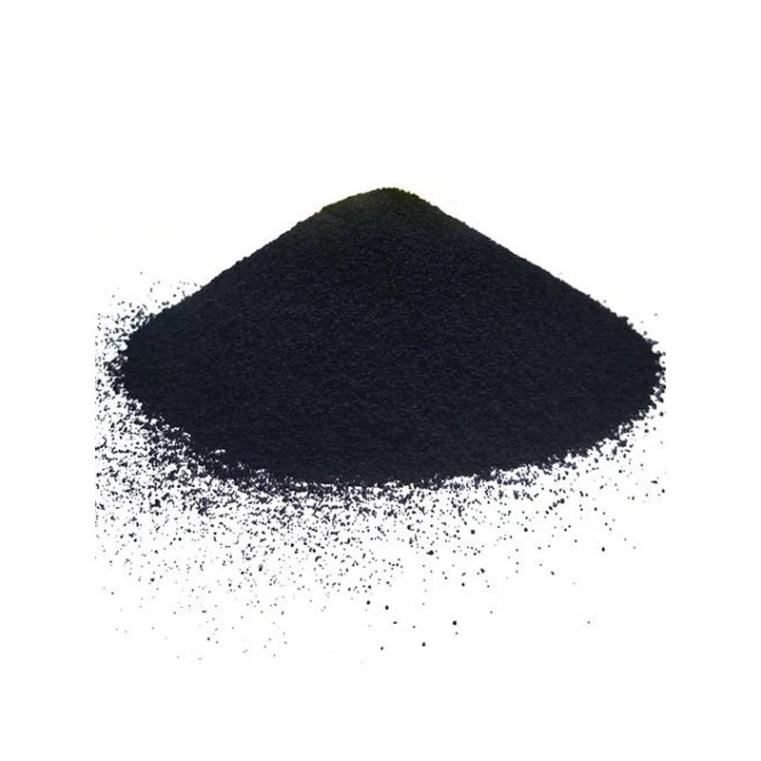
DTF black powder, known for its rich tones, primarily comprises carbon black and resins. Its deep shade renders it suitable for printing on darker substrates. Additionally, the fine grains of the powder facilitate excellent grip to fabrics, guaranteeing the printed design remains intact for an extended timeframe.
The makeup includes a blend of TPU rubber powder and activated carbon that synergistically preclude softening during printing. As a consequence, it has increased in popularity for efficiently printing on polyester, bags and other textiles susceptible to dye diffusion transfer. The merged formulation permits withstanding the heat typical of the printing process without compromising sharpness or spreading of the visuals placed on temperature-sensitive materials like polyester.
● Pros and Cons
Pros
- Appropriate for printing on darker cloth substrates.
- Provides superb grip to natural textiles like cotton for long-lasting designs.
- Fine powder composition allows for precise printing output.
- Compatibility with a variety of common printing machinery.
Cons
- Restricted suitability for light fabric backdrops may limit design options.
- Multiple applications sometimes needed to achieve brighter hues.
- Additional heat and pressure application potentially required to guarantee quality results.
- Risk of soiling and potential challenges cleaning intricate designs.
DTF White Powder
● What is DTF White Powder?
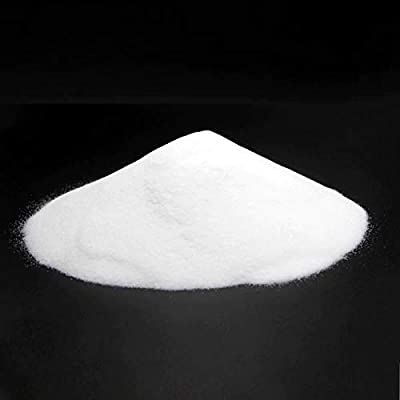
White DTF powder features a composition of titanium dioxide, resin and specific additives which grant its signature white tone. Unlike DTF black powder, white DTF powder contains larger pigment particles rendering it highly suitable for printing on lighter substrates. Additionally, white DTF powder demonstrates superb adhesive qualities, confirming designs placed on fabrics persist intact for an extended timeframe.
● Pros and Cons
Pros
- Appropriate for printing on lighter cloth substrates.
- Provides superb bonding to synthetic materials like polyester.
- Larger pigment particles allow for increased coverage with fewer coats.
- Compatible with various common pressing/printing equipment.
Cons
- Restricted suitability for dark fabric backdrops may confine design options.
- Multiple applications sometimes needed to achieve deeper hues.
- Additional heat and pressure application potentially required to guarantee quality results.
- Risk of soiling and potential challenges cleaning intricate designs.
How to Use DTF Powder?
DTF powder can be applied either by hand shaking or machine shaking. Though the printing outcomes prove quite similar, the choice of manual versus automated application could influence productivity and costs relying on the specific production workflow involved. Before deciding, it merits investigating both techniques further to appreciate the nuances and suitability for a given production line or project. Learning more about these two potential powder dispersal techniques may aid in selecting the approach optimizing operations in a given context.
● Oven
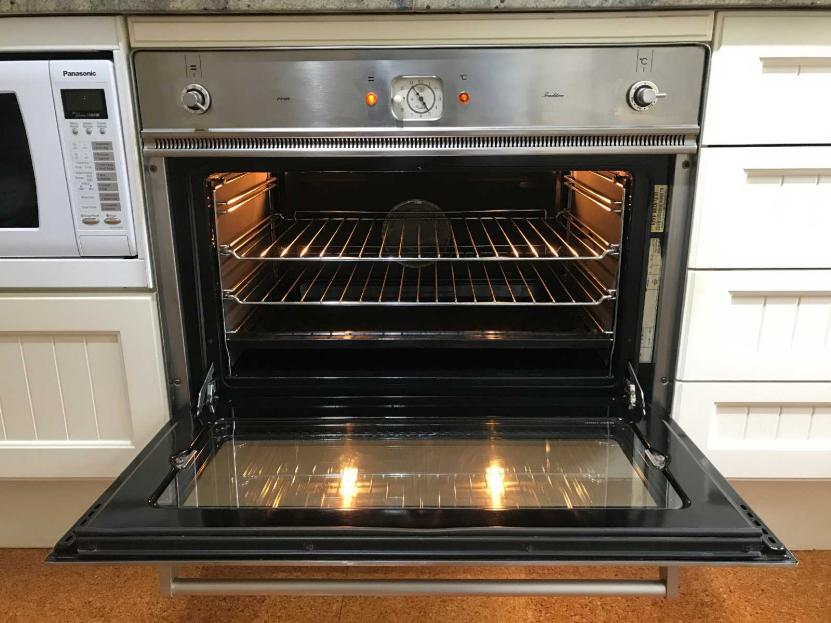
Getting started with DTF typically involves setting up a customized printer, furnace and heat press. The critical phase of dispersing powder atop the newly printed region must immediately ensue. However, as human handling is required at this point, attaining consistent powder placement across large yields can be difficult. Moreover, if solely dependent on such equipment exclusivity to undertake DTF tasks opposed to mechanical alternatives upcoming, higher costs inevitably materialize in the forms of increased monetary outlay, longer throughput and additional manual intervention necessities.
● Powder Shaker
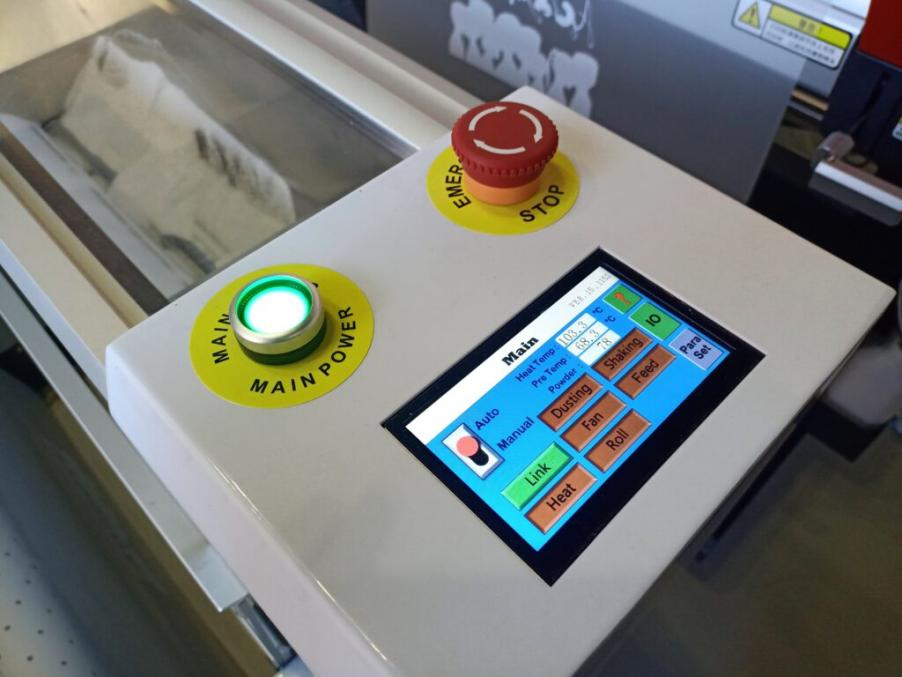
Generally, the DTF printer integrates with a self-sufficient powder shaker. For newcomers’ first views, the pairing may appear to represent the complete setup. However, the mechanical powder shaker works autonomously to reliably and evenly spread powder over films on average, then expedites heating without human handling. Additionally, it is gentle when rolling films to shield patterns. Consequently, massive reductions in manual effort are attainable. Also, the automated process keeps printed patterns immaculate. All said, the final outputs are of outstanding quality overall.
How Does DTF Powder Work?
In fact, DTF powder can also appropriately be termed adhesive powder. The DTF powder constitutes a solidified glue presented in particulate form. Once films acquire an even layer of powder via a distribution machine, the granules melt upon heating to transform into a plastic film. This newly generated plastic layer enables transference of the design onto substrates. When progressed through the heat press, the plastic film becomes tacky yet indiscriminate in its selection of textile materials as the receiving surface. Therefore, substrate fabric variety becomes an non-restrictive consideration, relieving concerns over compatibility.
A Comparative Analysis: DTF Black Powder vs. White Powder
The primary differences between black and white DTF powder relate to their shade, pigment size, fabric compatibility, adhesive properties, and potential need for extra layers.
Color is the most obvious distinguishing factor, with white exhibiting a pure white hue compared to black’s darker tone.
Particle size also varies, as white contains larger grains relative to black’s smaller pigments. This impacts coverage uniformity and print definition.
Fabric type heavily influences suitability, as black works best on darker textiles while white is more appropriate for lighter ones.
Adhesion abilities also differ, with white bonding strongly to synthetics and black adhering well to natural fibers.
Achieving vibrant hues may sometimes necessitate supplemental applications for both, although black may demand more due to its darker base.
Proper selection relies on hands-on testing with an assortment of materials to identify which best fits specific needs. Only through experimentation can an informed decision be made around which powder optimally suits various printing applications.
Conclusion
Black and white powders each have their own composition affecting printed outputs. Choosing the right powder depends on several production factors.
Black powder contains tiny pigments absorbing many light wavelengths, appearing deep black. It firmly embeds designs on fabrics after heating. However, its darkness may hinder coloring visibility on prints.
White powder has larger particles reflecting more light. This enhances color brightening when combined with inks or dyes. During heating, its composition penetrates fabric compositions like synthetics well while allowing intricate patterns clearer definition.
Both powders continue customized development. Scientists experiment new formulations balancing pigment properties. Updated powders may bond fasters, work on broader materials, or facilitate more vivid shades.
Manufacturers adopting digital powder printing analyze application needs deciding the better powder match. Black serves projects demanding opacity or durability on darker fabrics. White excels for lightweight, light-colored bases needing color strengthening or higher printing clarity.
Staying current lets creators leverage powder innovations. They review formulation changes benefiting goal types. By learning each powder’s specialized capabilities and limitations, users tailor the right selection per project or product line for optimized results.